Did you know that computed tomography (CT) is one of the leading technologies in industrial measurement technology in mechanical engineering? By using CT, companies can carry out precise measurements and optimize quality control. CT is used for the non-destructive testing of components and enables 3D X-ray inspection. CT inspection systems offer solutions for mechanical engineering to speed up inspection processes and increase production output.
Key findings:
- CT is a leading technology in industrial measurement technology in mechanical engineering.
- CT enables precise measurements and optimizes quality control.
- 3D X-ray inspection with CT offers deeper insights into components.
- CT inspection systems speed up inspection processes and increase production output.
- CT is indispensable for mechanical engineering and will continue to play a decisive role in the future.
General challenges of measurement technology in mechanical engineering
Measurement technology in mechanical engineering faces various challenges. One of the main problems is the size of the components to be measured. Often, these measurements cannot be carried out in a conventional measuring room, as the dimensions of the components exceed the available space.
Another obstacle is the difficult measuring environment. In industrial production, the machine room and working environment are often confronted with dust, oil and other contaminants. In addition, the temperatures in the environment vary, which can have an impact on the measurements.
Robust measurement technology is required to meet these challenges. The devices must not only offer resistance to dirt, but must also be able to compensate for vibrations in order to carry out precise measurements. Precision is crucial, as even the smallest deviations and measurement errors can have serious consequences, such as damage to the components or even their failure.
Quality assurance in mechanical engineering with ZEISS measuring devices
ZEISS offers comprehensive quality assurance solutions for mechanical engineering, including industrial CT systems and versatile coordinate measuring machines. With ZEISS metrology, companies can accurately capture and analyze measurement data to ensure consistent product quality.
CT component analysis plays a central role in quality assurance. With the help of CT inspection systems, components can be analyzed non-destructively and measurements can be carried out during production. This enables a comprehensive inspection of components and ensures compliance with specifications. ZEISS supplies reliable measuring systems that deliver precise and reproducible results.
ZEISS software solutions are also an important part of quality assurance in mechanical engineering. ZEISS CALYPSO provides companies with powerful software that can be used to record, process and analyze measurement data. This software enables efficient data processing and optimizes the entire measurement process.
Quality assurance in mechanical engineering is crucial for product quality and customer satisfaction. With ZEISS measuring instruments, companies can ensure that their products meet the highest quality standards. Through precise measurements and effective quality assurance, they can strengthen their competitiveness and gain the trust of their customers.
With ZEISS measuring systems, companies in the mechanical engineering sector rely on innovative technologies to optimize their production processes and ensure the quality of their products. Industrial CT and coordinate measuring machines from ZEISS offer a reliable solution for quality assurance in mechanical engineering and enable efficient production control.
CT applications in mechanical engineering
The applications of computed tomography (CT) in mechanical engineering are extremely diverse and offer numerous advantages for companies. One of the main applications is CT component analysis, which makes it possible to perform precision measurements and detect various defects such as porosities, cracks and other irregularities.
With the help of CT component analysis, mechanical engineering companies can obtain precise information about the structure and properties of components. This is particularly important for quality assurance and optimizing the manufacturing process. By geometrically comparing CT scans with digital 3D CAD models, deviations can be identified and the manufacturing process optimized.
Another major advantage of CT in mechanical engineering is the ability to examine connections, internal structures and embedded parts. CT enables non-destructive testing in which the component remains intact and still allows detailed insights.
To better understand CT applications in mechanical engineering, it is helpful to visualize the CT scans.
Here are sample images for CT scans of a component in mechanical engineering:
Internal analysis of a component
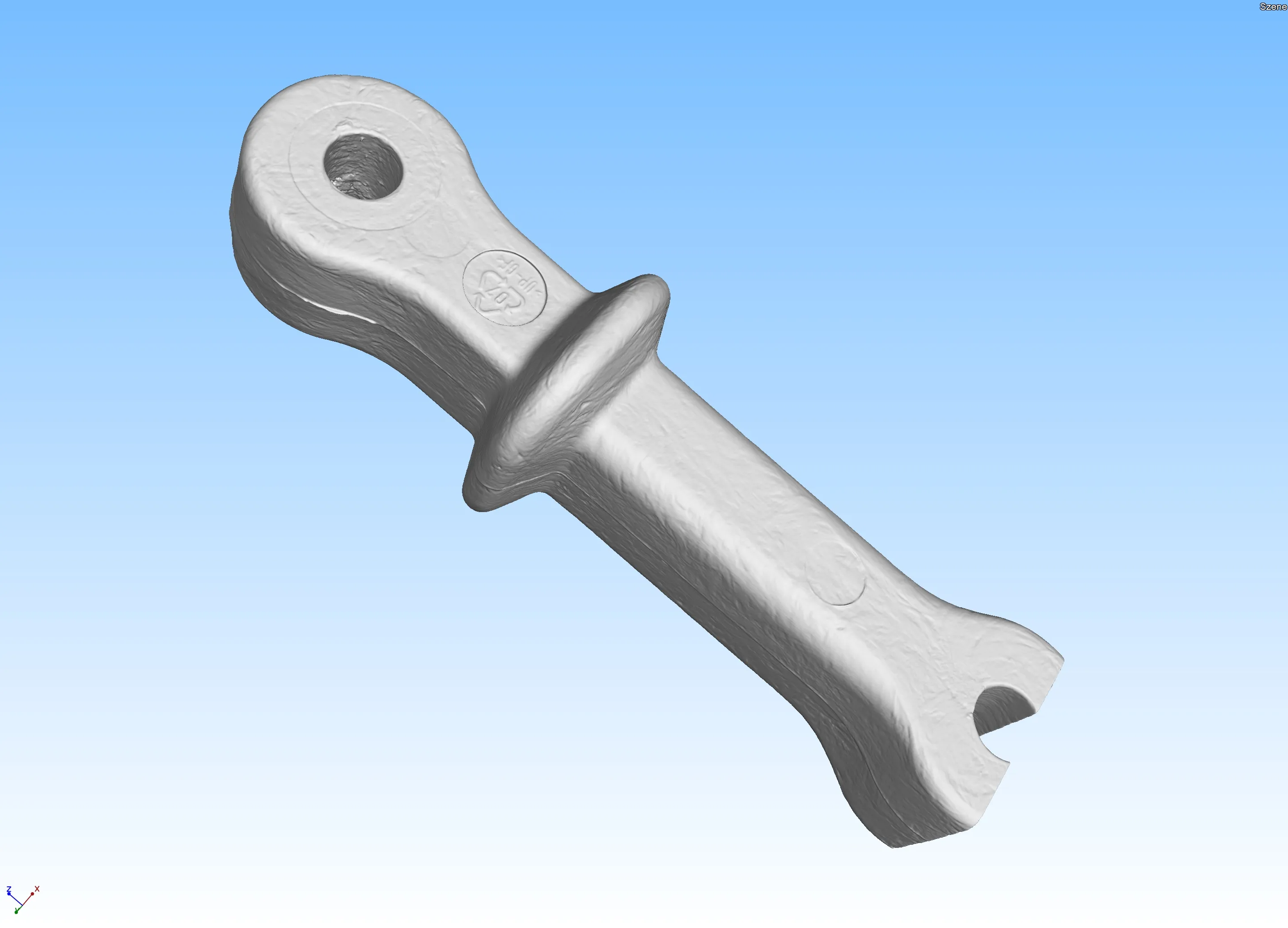
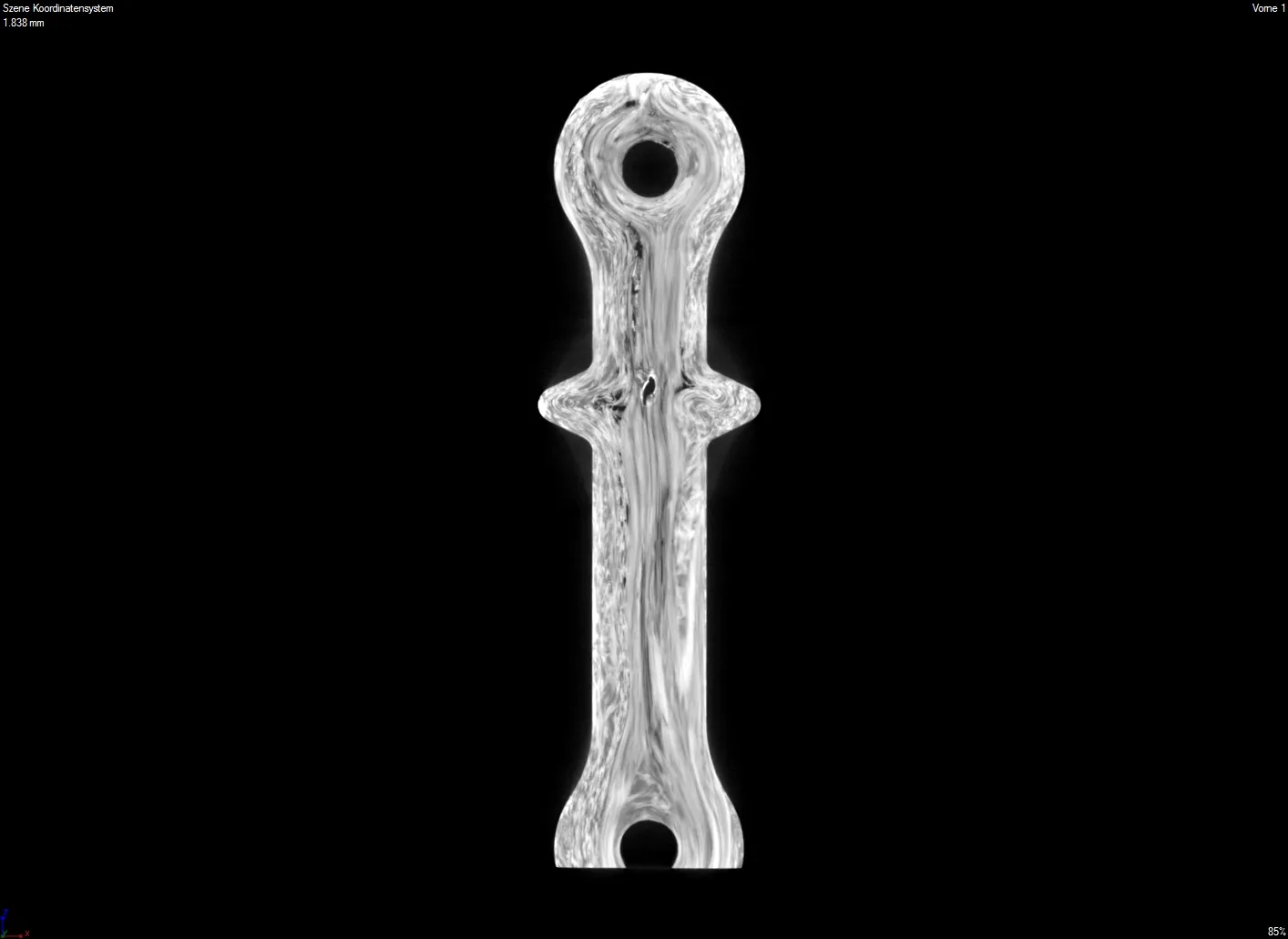
Blowhole & porosity analysis of a die-cast component
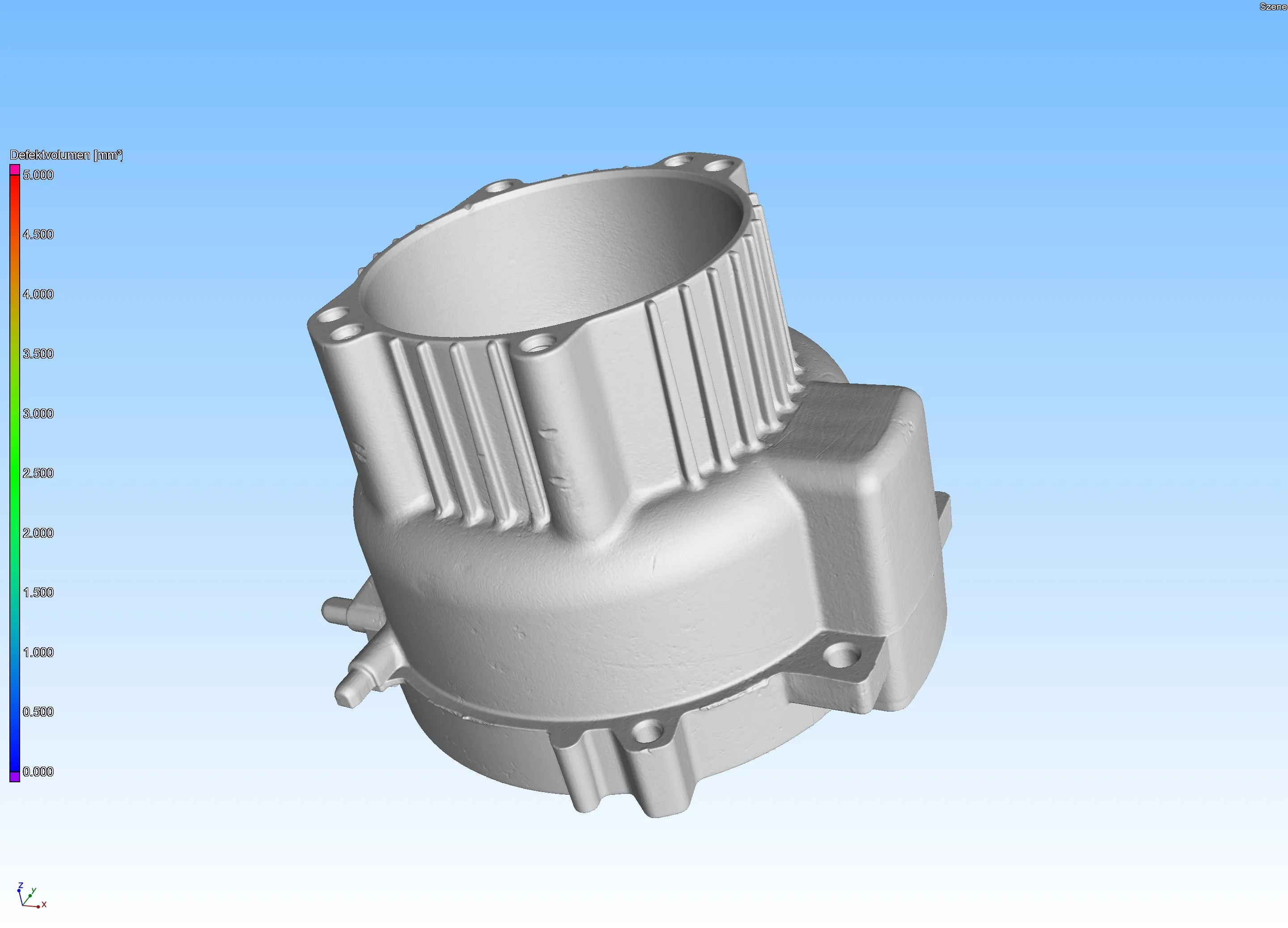
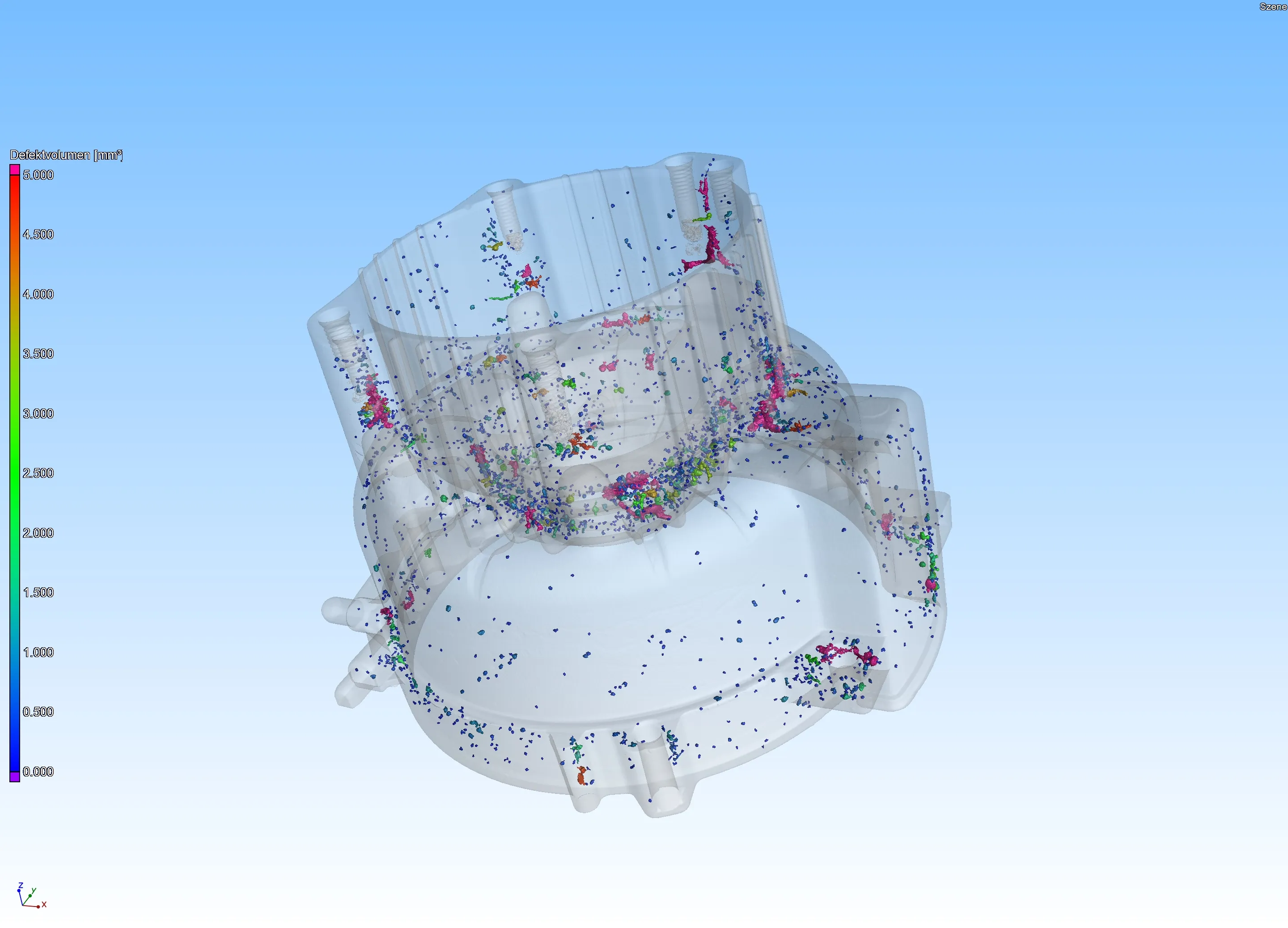
Defect analysis of a component (detection of a crack that is not visible from the outside)
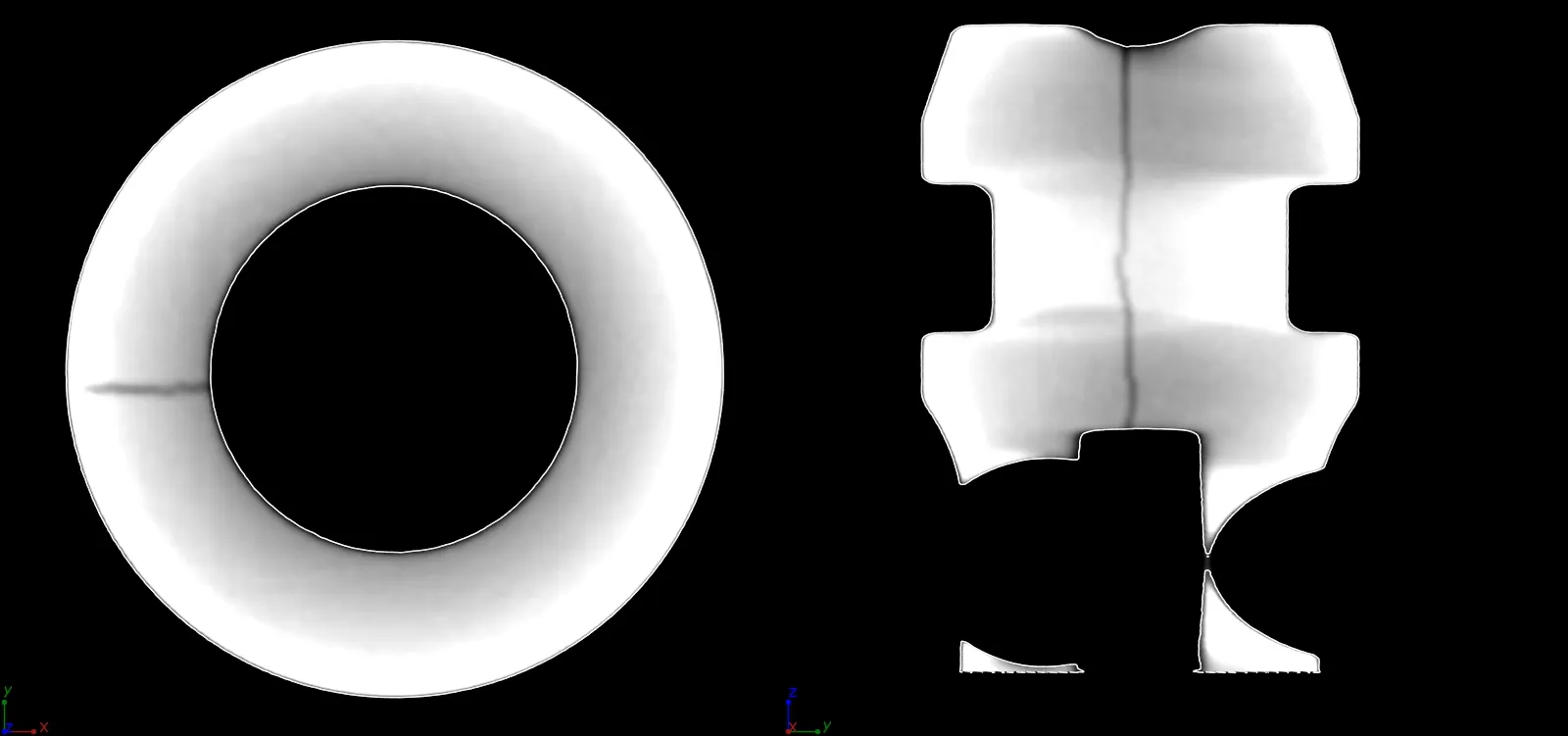
Analysis and representation of an assembly of several materials (threaded spindle)
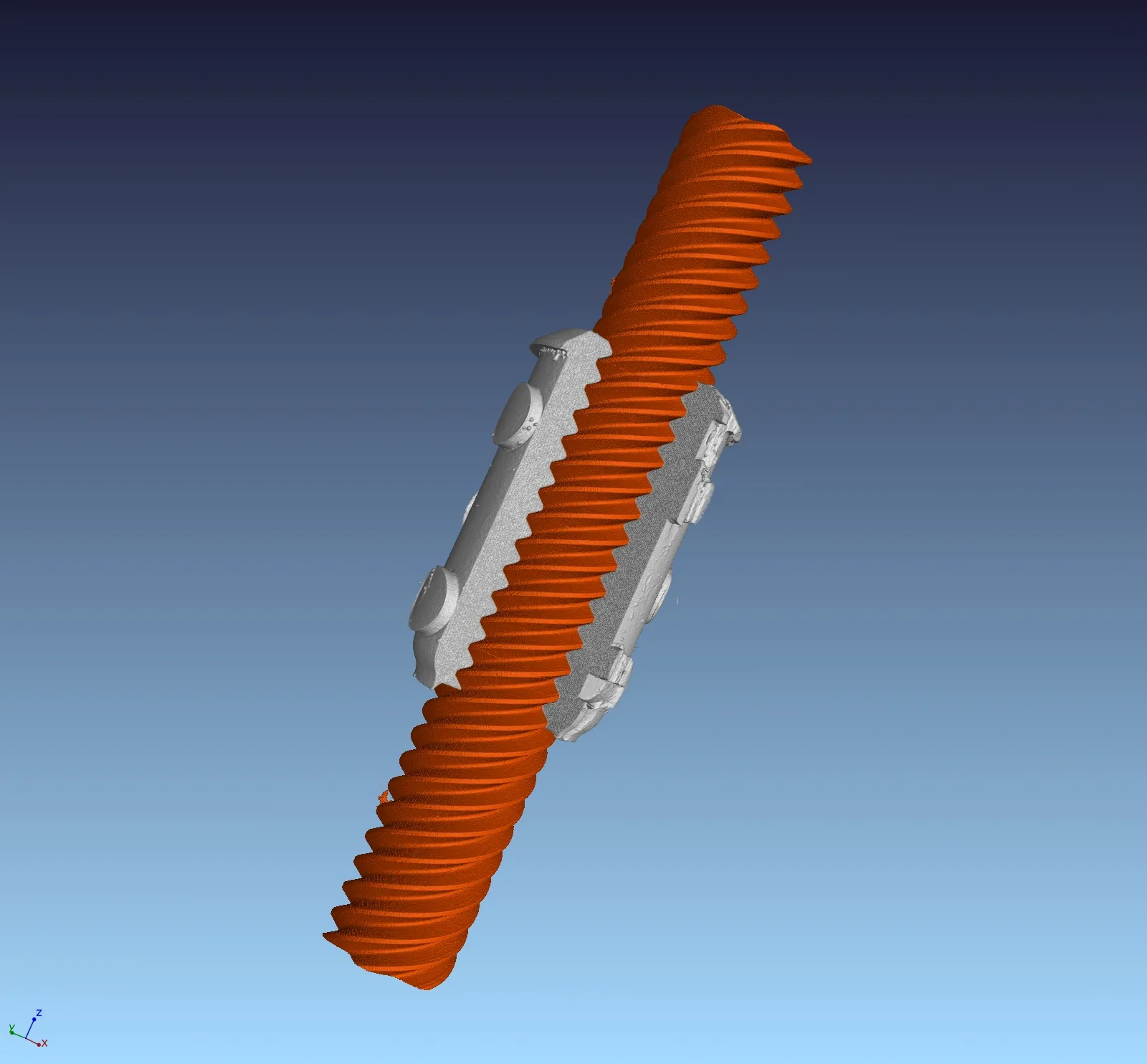
As can be seen in the CT scan, CT provides detailed information about the internal structures of the component. This enables precise examination and analysis in order to detect possible defects or deviations.
Overall, CT applications in mechanical engineering offer a comprehensive opportunity for quality assurance, precision measurements and optimization of the manufacturing process. By using CT inspection systems, companies can improve their product quality and work more efficiently.
Advantages of CT in mechanical engineering
Computed tomography (CT) offers numerous advantages in mechanical engineering. Non-destructive testing allows components to be checked for quality and integrity at the end of the production process. This enables effective quality control and minimizes the risk of faulty products.
CT can be used to perform precise measurements that ensure high accuracy and reliability. This enables companies to ensure that their products meet the specified requirements and fulfill quality standards.
CT component analysis also optimizes the manufacturing process. By examining the components in detail, possible weak points can be identified and improved. This increases efficiency and enables the production of high-quality products.
With CT measurement technology, inspections can be carried out more quickly as no complex iteration loops are required. This speeds up the entire inspection process, resulting in more efficient production.
Advantages of CT in mechanical engineering
- Non-destructive testing of components
- Precise measurements for high product quality
- Optimization of the production process
- Increased efficiency through fast inspections
Areas of application for CT in mechanical engineering
CT (computed tomography) is used in various areas of application in mechanical engineering. It plays a decisive role in the quality control of components and enables precise detection of internal structures as well as comprehensive product analysis.
Automotive industry
In the automotive industry, CT is used to inspect components such as engine blocks, plastic components or battery cells. The 3D X-ray inspection enables the precise detection of cavities, cracks and defects to ensure product quality.
Aerospace
In the aerospace industry, CT plays an important role in the inspection of aircraft and spacecraft components. Thanks to CT component analysis, complex lightweight structures can be analyzed to ensure that they meet the high requirements and safety standards.
Electronic components
CT is also used to inspect electronic components such as circuit boards and chips. By precisely measuring distances and connections, quality problems can be detected and rectified at an early stage to ensure that electronic devices function flawlessly.
Metal processing
In metal processing, CT enables the precise examination of metal structures and the measurement of wall thicknesses, especially of aluminum components. This is particularly important in the production of safety-critical components. CT analysis can be used to identify possible defects and faults in order to improve the quality of the components.
CT inspection systems are also used in other areas such as the analysis of injection molded parts and additive manufacturing. CT in mechanical engineering provides accurate measurement results and enables improved product quality by detecting defects at an early stage and increasing the efficiency of quality control.
CT component analysis is becoming increasingly important in mechanical engineering and has become an indispensable tool for manufacturing high-quality and safe products.
CT scan data and its use in industry
CT scan data is extremely valuable for companies in the mechanical engineering sector as it provides detailed geometric information about components. This data enables precise analyses, metrological evaluations and the identification of deviations. Wall thickness analysis in particular is an important area of application.
Companies can use CT scan data to carry out precise measurements and monitor the quality of their products. The data makes it possible to compare components with digital 3D CAD models and identify deviations. This enables companies to optimize their manufacturing processes and continuously improve product quality.
One example of the use of CT scan data is the precise analysis of wall thicknesses. The metrological evaluation of CT scan data enables companies to precisely determine the wall thickness of components and identify potential weak points or material defects. This enables early intervention and ensures high product quality.
To illustrate the use of CT scan data, here is an example of a wall thickness analysis:
By systematically evaluating such data, companies can identify patterns and solve potential problems at an early stage. This leads to effective quality control and reduced waste.
The precise analysis of CT scan data and metrological evaluation are important tools for companies in the mechanical engineering sector. They provide a solid basis for product optimization and contribute to increasing product quality and efficiency.
Possibilities for performance optimization with CT in mechanical engineering
Computed tomography (CT) offers a wide range of possibilities for optimizing performance in mechanical engineering. Through precise measurements and comprehensive quality control, companies can improve their products and reduce waste. CT technology allows deviations and defects to be identified quickly, enabling efficient optimization of measurement procedures and quality assurance processes.
A key advantage of CT in mechanical engineering is that CT inspection systems can be seamlessly integrated into Industry 4.0. This opens up advanced possibilities for quality control and product analysis. By using big data and artificial intelligence, CT scan data can be efficiently analyzed and used to optimize manufacturing processes.
These possibilities for performance optimization with CT in mechanical engineering include
- Precise measurements: CT technology enables high-precision measurements that ensure high accuracy and quality assurance.
- Optimization of measurement processes: CT technology allows measurement procedures to be continuously improved and optimized in order to increase the efficiency and performance of measurements.
- Real-time monitoring: CT inspection systems can provide monitoring data in real time and thus detect faults or deviations at an early stage in order to be able to react quickly.
- Product analysis and fault detection: CT technology enables a detailed product analysis in which faults, weak points or defects in components can be identified.
- Increased efficiency: Companies can increase their efficiency and save valuable resources through precise measurements, quality control and optimization of production processes.
CT in mechanical engineering provides companies with powerful tools to improve their product quality and efficiency. By integrating CT technology into Industry 4.0, companies can gain a competitive advantage and further optimize their manufacturing processes.
Advantages of performance optimization with CT in mechanical engineering
- Improving product quality
- Reduction of waste
- Increasing the efficiency of production processes
- Quick identification of deviations and defects
- Optimization of the measurement methods
- Integrability in Industry 4.0
Conclusion
The use of computed tomography (CT) in mechanical engineering offers numerous advantages for companies. Through precise measurements and efficient quality control, companies can improve product quality and optimize their manufacturing processes. CT technology enables deeper insights into components and offers non-destructive testing, resulting in fewer rejects and cost savings.
CT inspection systems in mechanical engineering enable precise analysis of components and help to detect defects, cracks and porosity. This helps companies to ensure the quality of their products and increase customer satisfaction. By using CT measurement technology, companies can also improve the precision of their measurements and ensure compliance with design specifications.
CT technology has established itself as an indispensable tool in mechanical engineering and will continue to play a crucial role in the future. It offers companies valuable insights, improved quality control and more efficient workflows. With the benefits of CT metrology, mechanical engineering companies can strengthen their competitiveness while meeting precision and quality requirements.
FAQ
What advantages does CT offer in mechanical engineering?
CT enables non-destructive testing of components, precise measurements and high product quality. It also optimizes the manufacturing process and helps to increase efficiency.
What role does CT component analysis play in quality assurance?
CT component analysis plays a central role in quality assurance. CT inspection systems can be used to analyze components non-destructively and carry out measurements during production.
In which areas is CT used in mechanical engineering?
CT is used in various sectors such as the automotive industry, aerospace, electronic components and metal processing. It enables the quality control of components, 3D X-ray inspection to capture internal structures and comprehensive product analysis.
How can CT scan data be used in mechanical engineering?
CT scan data provides detailed geometric information about components. Companies can use this data to carry out precise analyses, perform metrological evaluations and identify deviations.
How can CT be used to optimize performance in mechanical engineering?
Through precise measurements and quality control, CT in mechanical engineering can help companies to improve their products and reduce rejects. It enables deviations to be identified quickly and measurement processes to be optimized.
What advantages does CT in mechanical engineering offer companies?
CT in mechanical engineering enables precise measurements, non-destructive testing, product quality and a more efficient way of working. It is an indispensable tool for ensuring the quality of components.
What is the significance of CT inspection systems in industry?
CT inspection systems offer advanced possibilities for quality control and product analysis. They can be integrated into Industry 4.0 and support performance optimization.
What are the challenges of measurement technology in mechanical engineering?
Measurement technology in mechanical engineering faces challenges such as the size of the components to be measured and a demanding measurement environment. The measurements must be precise and robust in order to deliver accurate results.
How can ZEISS help with quality assurance in mechanical engineering?
ZEISS offers quality assurance solutions for mechanical engineering with industrial CT and various coordinate measuring machines. The measurement technology from ZEISS enables accurate acquisition and analysis of measurement data to ensure consistent product quality. At Q-Tech Roding, we work exclusively with the market leader ZEISS to ensure the best quality.