Bauteilvermessungen leisten einen entscheidenden Beitrag zur Qualitätssicherung in der Industrie. Dabei ist der Prozess recht umfangreich und kann je nach Messmethode und Messgerät stets variieren - ein absolut wichtiger Vorgang, um die Kundenanforderungen zu erfüllen.
Was verstehen Experten unter einer Bauteilvermessung? Die Bauteilvermessung dient der Überprüfung von geometrischen Eigenschaften wie Maßhaltigkeit, Form- und Lage, Rundheit und Oberflächenbeschaffenheit von Bauteilen. Während des Vorgangs kommen eine ganze Reihe von Messmethoden und Messgeräten zum Einsatz. Hochqualifizierte Fachkräfte nutzen Koordinatenmessgeräte, optische Messsysteme oder auch Röntgenstrahlung.
Sie wollen wissen, welche Technik bei uns im Hause Q-Tech zum Einsatz kommt? Dann werfen sie einen Blick auf unser Equipment.
Die Bedeutung der Bauteilvermessung
Die Präzision einer Bauteilvermessung ist von entscheidender Bedeutung, um sicherzustellen, dass das gefertigte Bauteil den Anforderungen entspricht. Dadurch wird eine gleichbleibende, hohe Qualität gewährleistet.
Anderenfalls kann es zu Ausschuss, Nacharbeit, Kundenbeschwerden und manchmal auch zu Sicherheitsproblemen kommen. Diese Umstände verursachen unangenehme Kosten und schmälern den Gewinn eines Unternehmens.
Eine genaue Bauteilvermessung hingegen führt zu einer Erhöhung der Wirtschaftlichkeit, einer Reduzierung der Fehlerquote und zu einer besseren Zufriedenheit bei dem Kunden.
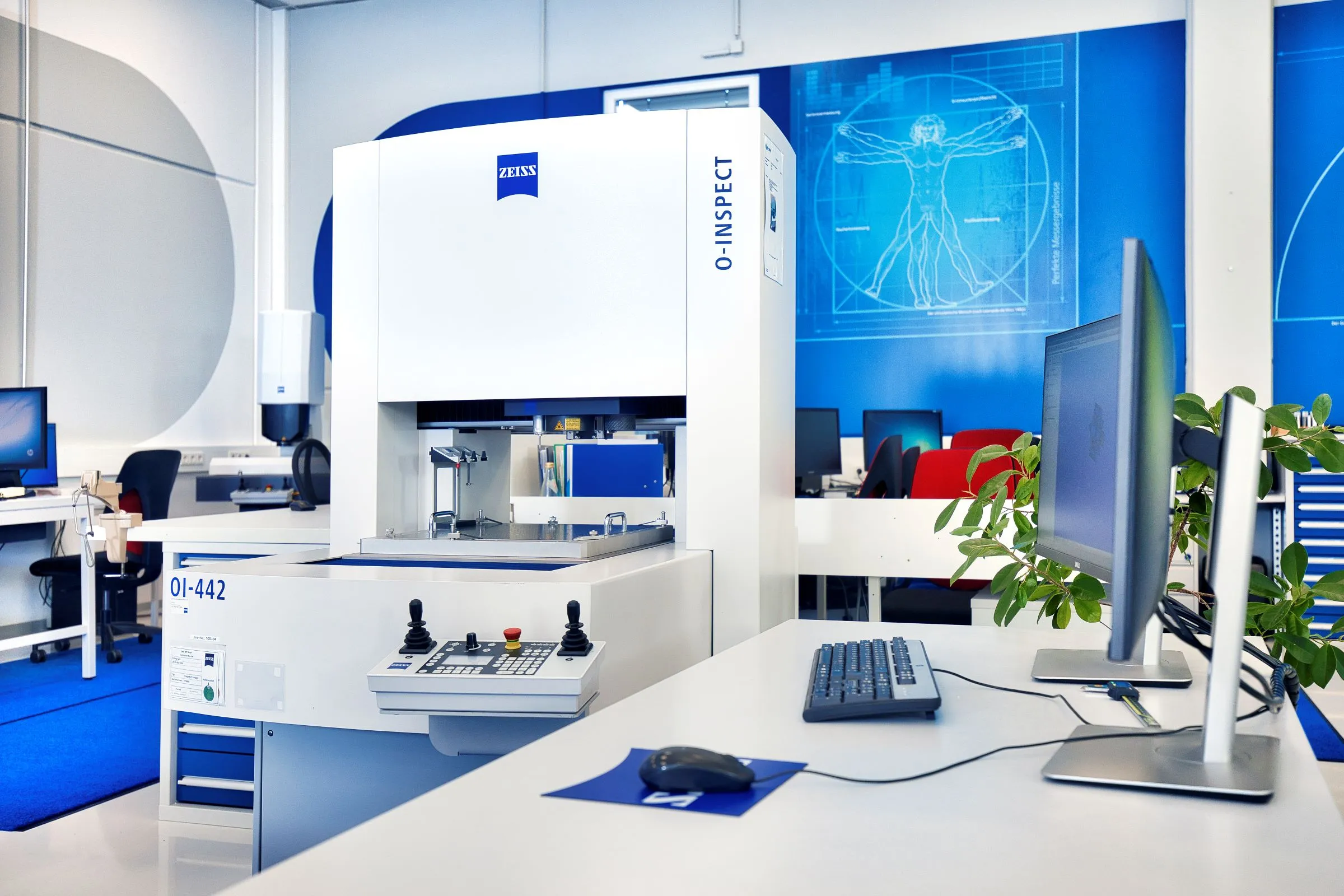
Funktionsweise
Der Ablauf bei der Bauteilvermessung lässt sich in mehrere Schritte einteilen. Die einzelnen Phasen können je nach Messmethode und Messgerät variieren. Zu Beginn spannt der Prüfer das zu prüfende Bauteil in das Messgerät ein bzw. positioniert dieses darauf.
Anschließend findet die eigentliche Messung statt, bei der das Bauteil gemessen wird und alle relevanten geometrischen Eigenschaften erfasst werden. Hierzu ist es häufig nötig, die Messung in verschiedenen Positionen durchzuführen.
Die Messergebnisse werden daraufhin mit einer Auswertesoftware analysiert und mit den vorgegebenen Toleranzen abgeglichen. Kommt es zu Abweichungen, klassifiziert der Prüfer das Bauteil als fehlerhaft. Dieses muss dann entweder nachgearbeitet oder aussortiert werden.
Vorteile einer Bauteilvermessung
Angewendet, bietet der Prozess eine ganze Reihe von Vorteilen:
- Hohe Präzision: Der Ist-Zustand geometrischer Eigenschaften eines Bauteils wird präzise messbar gemacht.
- Effizienz: Aufgrund der präzisen Messung sinkt die Fehlerquote, weil so Ausschuss vermieden wird. Das erhöht die Wirtschaftlichkeit und Effizienz in der Fertigung.
- Qualitätssicherung: Eine präzise Bauteilvermessung trägt einen entscheidenden Teil dazu bei, eine konstant hohe Qualität bei den gefertigten Bauteilen zu gewährleisten. Insbesondere bei sicherheitskritischen Anwendungen in der Luft- und Raumfahrt, der Automobilindustrie oder der Medizintechnik spielt der Punkt eine wichtige Rolle.
- Kundenzufriedenheit: Weil die gelieferten Bauteile den geforderten Anforderungen entsprechen, können die Kunden sich sicher sein, dass die Funktionalität absolut gegeben ist. Das erhöht die Kundenzufriedenheit.
- Kosteneinsparungen: Eine genaue Bauteilvermessung führt zu Kosteneinsparungen, weil die Fehlerquote reduziert wird und somit weniger Ausschuss und Nacharbeit nötig ist.
Bauteil scannen - Welche Methoden kommen zum Einsatz?
Beim Bauteil scannen kommen unterschiedliche Messmethoden und Messgeräte zum Einsatz - abhängig von den spezifischen Anforderungen und Eigenschaften der zu prüfenden Bauteile.
Hier sind einige der bekanntesten Messmethoden:
- Koordinatenmessgeräte: Koordinatenmessgeräte ermöglichen eine hochpräzise und dreidimensionale Vermessung von Bauteilen. Die Geräte finden sich in vielen Industriegebieten wieder und werden dort häufig genutzt.
- Optische Messsysteme: In der optischen Messtechnik verwenden die Prüfer verschiedene Sensoren und Kameras, um die geometrischen Eigenschaften von Bauteilen zu erfassen. Oberflächenbeschaffenheit, Rauheit, aber auch Form- und Lagetoleranzen lassen sich mit dieser Methode einwandfrei bestimmen.
- Röntgenstrahlung: Diese Technik eignet sich besonders gut, um innere Strukturen und Eigenschaften von Bauteilen zu erfassen, die mit anderen Messmethoden nur schwer zu untersuchen sind. Röntgenstrahlung kommt in der Automobilindustrie, der Luft- und Raumfahrt und der Elektroindustrie zum Einsatz.
- Ultraschall: Mit der Ultraschall-Methode lässt sich die Dicke von Materialien und die Qualität von Schweißnähten messen. Ultraschallmessungen werden häufig in der Schwerindustrie und der Chemieindustrie eingesetzt.
- Streifenprojektion: Bei dieser Methode wird ein Lichtmuster auf das zu prüfende Bauteil projiziert und die Verzerrungen des Musters werden gemessen. Das geschieht, um das Bauteil vollständig zu digitalisieren und dann am digitalen Abbild Messungen durchzuführen. Die Streifenprojektion kommt häufig bei der Herstellung von Glas und Kunststoff zum Einsatz, wird aber auch in der Elektroindustrie oder im Maschinenbau eingesetzt.
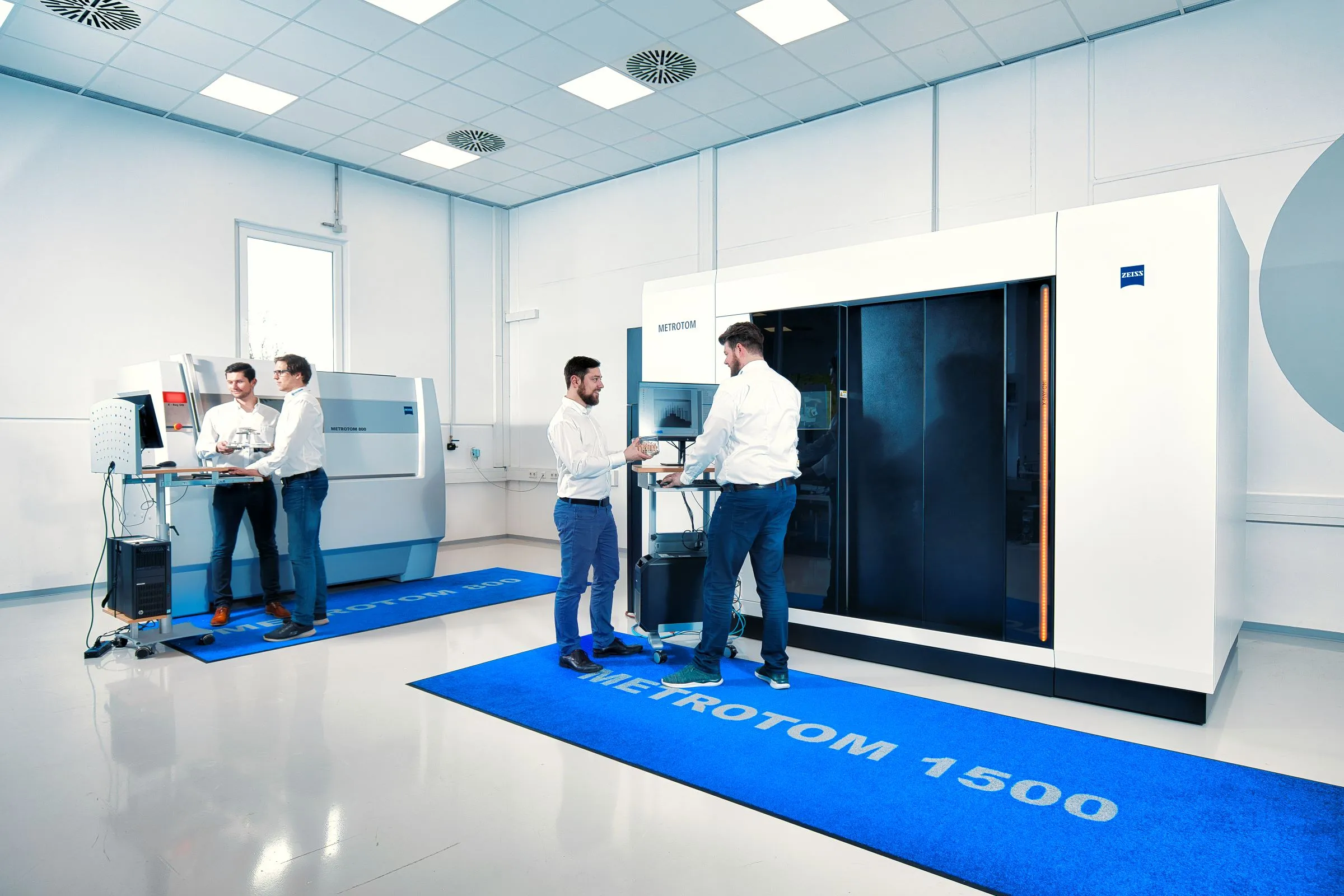
Messverfahren im Hause Q-Tech
Im Folgenden erhalten Sie einen Überblick, welche Verfahren wir bei uns anbieten.
Bedenken Sie, dass es nicht “das Eine” Messverfahren zur Überprüfung von physikalischen Größen gibt - im Gegenteil, manchmal lohnt es sich mehrere Messverfahren miteinander zu kombinieren, um ein aussagekräftiges Bild über den funktionalen Zustand des Bauteils zu erhalten.
Computer tomography
Eine Computertomografie öffnet mittels Röntgenstrahlen den Blick in das Innere eines Bauteils, ohne es zerstören zu müssen. Der Prüfling kann auch nach der Messung weiterhin verwendet werden.
Dadurch lassen sich verborgene Defekte aufzeigen und analysieren, die zum Beispiel Koordinatenmessgeräte nicht ohne Weiteres erfassen können. Beispiele sind Einschlüsse, Lunker oder innere Bauteilfehler. Hinzu kommt, dass auch weiche und transparente Materialien messbar sind.
Für alle Bauteile kann der Prüfer daraus ganze CAD-Modelle mit sämtlichen Innen- und Außenstrukturen erstellen oder die gescannten Bauteile auch einfach reproduzieren. Dieser Prozess ist Teil des Reverse Engineerings.
Q-Tech nutzt für die Computertomografie die Maschinen ZEISS METROTOM 800 und den ZEISS METROTOM 1500 G3.
Taktile Koordinatenmesstechnik
Diese Technik basiert auf der Antastung eines Bauteils. Ein Taster nimmt die Oberflächenkonturen als Signale auf. Anschließend werden die Daten mit einer Software in XYZ-Koordinaten umgewandelt.
Unsere Messmaschinen arbeiten mit der Software CALYPSO. Wir setzen dabei auf die Qualität des Herstellers ZEISS.
In der 3D-Koordinatenmesstechnik nutzen unsere Prüfer die ZEISS PRISMO ULTRA, ZEISS PRISMO VERITY, ZEISS ACCURA II, ZEISS O-INSPECT 863 und die ZEISS ACCURA 7.
Häufig bestehen die Taster aus einem sehr harten Metall. Das Messergebnis enthält die Formabweichung des Tasters, Form- und Lageabweichungen des Prüfstücks und die Positionierfähigkeit des Koordinatenmesssystems.
Als Basis für die Koordination dient eine CNC-Steuerung. Mittels Korrekturfaktoren wird in allen drei Achsen ein stabiles Antastverhalten während der gesamten Messung garantiert.
Optical 3D digitization
Optische Vermessung von Bauteilen. Mit der optischen 3D-Digitalisierung kann von einem Bauteil ein digitaler Zwilling erstellt werden - das digitale Abbild eines materiellen Prüfstücks aus der realen Welt.
Für dieses Verfahren nutzen wir den GOM ATOS Q 8M. Dieser ist ein äußert vielseitig einsetzbarer LED-Scanner für kleine bis mittelgroße Bauteile.
Optische 2D-Vermessung
Ähnlichen wie bei der 3D-Digitalisierung kann hier das Prüfteil berührungslos gemessen werden.
Optische 2D-Verfahren eignen sich unter anderem für symmetrische und flache Bauteile.
Rauheitsvermessung
Die Rauheitsvermessung ist bei uns Teil der Koordinatenmesstechnik. Der Prozess läuft als 2D-Messung im Tastschnittverfahren ab. Genutzt wird ein taktiles Tastsystem, das punktuell die Objektoberfläche ganz genau durch Antasten erfasst.
Daraufhin erstellen wir einen Oberflächenschnitt und ein exaktes Profil. So können wir genau die Oberflächenstruktur Ihres Prüfobjektes feststellen.
Dieser Vorgang dient dazu, normgerecht alle Parameter der Rauheit und Welligkeit Ihres Bauteils zu erfassen.
Konturvermessung
Bei der Kontur bzw. Geometriemessung von Bauteilen machen wir keine Abstriche: Kanten, Radien und Winkeln sind in den vielen Fällen kritische Merkmale an einem Bauteil, wenn es um die Funktionalität geht. Die Geometrien werden von uns präzise und reproduzierbar erfasst - auch über große Messstrecken.
Die Ergebnisse erhalten Sie in Form einer 2D-Darstellung mit maßlicher Auswertung in grafischer Ausführung. Abweichungen sind bereits auf den ersten Blick erkennbar.
Als Messgerät kommt ein ZEISS SURFCOM NEX 031 SD-14 N zum Einsatz.
Zahnradvermessung
Die Zahnrad- oder auch Verzahnungsmessung führen wir mit unserer hochgenauen ZEISS Prismo ultra und dem integrierten Drehtisch in unserem Feinmessraum durch.
Unsere Verzahnungsmessung erfolgt auf einem hochpräzisen Niveau. Der ganze Vorgang geschieht taktil und ermöglicht die Auswertung von Innen- und Außenverzahnungen für nahezu alle Arten von Zahnrädern. Dabei spielt es keine Rolle, ob diese gerade, schräg oder konisch sind.
Bereits innerhalb von wenigen Minuten entsteht ein Messprotokoll mit allen geometrischen Eigenschaften. Die anschließende Analyse erfolgt ganzheitlich nach gängigen Normen.
Q-Tech: Ihr Partner für eine genaue Bauteilvermessung
Q-Tech ist ein führender Anbieter in der Messtechnik und sticht durch seine langjährige Erfahrung in der Bauteilvermessung heraus. Die hoch qualifizierten Ingenieure und Techniker aus unserem Hause verfügen über das nötige umfangreiche Fachwissen und setzen modernste Messmethoden und Maschinen ein, um eine präzise Bauteilvermessung zu realisieren.
Wir bieten unseren Kunden zugeschnittene Lösung für Ihre spezifischen Anforderungen und leisten dadurch einen wertvollen Beitrag für die Optimierung Ihrer Fertigungsprozesse. Optische Vermessung von Bauteilen und vielem mehr.
Conclusion
Die Bauteilvermessung leistet einen entscheidenden Beitrag zur Qualitätssicherung. Dank dieses Vorgangs können einzelne Bauteile auf ihre Funktionalität hin überprüft werden.
Im optimalen Fall werden so die Anforderungen des Kunden erfüllt.
Q-Tech ist auf diesem Gebiet Ihr zuverlässiger Ansprechpartner, der Ihnen genaue Messungen auf Experten-Niveau anbietet. Wenden Sie sich jederzeit an uns - die Maschinen und die Messtechniker im Hause Q-Tech arbeiten mit einer unvergleichlichen Präzision, die Sie anderswo nur schwer finden werden.