Die industrielle Computertomographie (iCT) revolutioniert die Industrie. Diese fortschrittliche Technologie ermöglicht es uns, in das Innere von Objekten zu schauen, ohne sie physisch zu zerlegen oder zu beschädigen. Aufgrund ihrer Eigenschaften wird sie neben der Industrie auch in der Medizin eingesetzt. Sie erlaubt eine detaillierte Prüfung und Analyse verschiedener Materialien und Komponenten.
Welche Vorteile bietet diese Technologie und wie wird sie in der Praxis eingesetzt? Die industrielle Computertomographie ist ein bildgebendes Verfahren, das dreidimensionale Bilder von der inneren Struktur eines Objekts erstellt. Sie wird in einer Vielzahl von Industriezweigen eingesetzt, die von der Automobil- bis zur Luft- und Raumfahrtindustrie reichen. Somit lässt die industrielle Computertomographie präzise Messungen eines Bauteils zu.
Sie wollen mehr zu unseren einzelnen Computertomografen erfahren? Dann werfen Sie gerne einen Blick auf unsere Software & unser Equipment.
Was ist Industrielle Computertomographie?
Die industrielle Computertomographie (CT) zählt zu den zerstörungsfreien Prüfverfahren aus der Messtechnik, die in der Industrie und im technischen Sektor zur Überprüfung und Analyse verschiedener Komponenten und Materialien eingesetzt werden. Sie arbeitet mit der Erzeugung und Verarbeitung von Röntgenstrahlen, die einen Gegenstand durchdringen.
Durch dieses Verfahren kann die CT ein detailliertes 3D-Bild des inneren Aufbaus eines Objekts liefern. Das erlaubt eine tiefgehende Untersuchung von innen, ohne das Objekt physisch zu zerstören oder zu öffnen.
Die resultierenden Bilder des Bauteils sind hochauflösend. Dadurch kann der Prüfer Mängel, Fehler oder andere Merkmale identifizieren.
Die industrielle Computertomographie ist in zahlreichen Branchen weit verbreitet. Dazu gehören zum Beispiel die Automobilindustrie sowie die Luft- und Raumfahrt. In diesen Bereichen spielt sie in der Qualitätssicherung, Produktentwicklung und Forschung eine entscheidende Rolle.
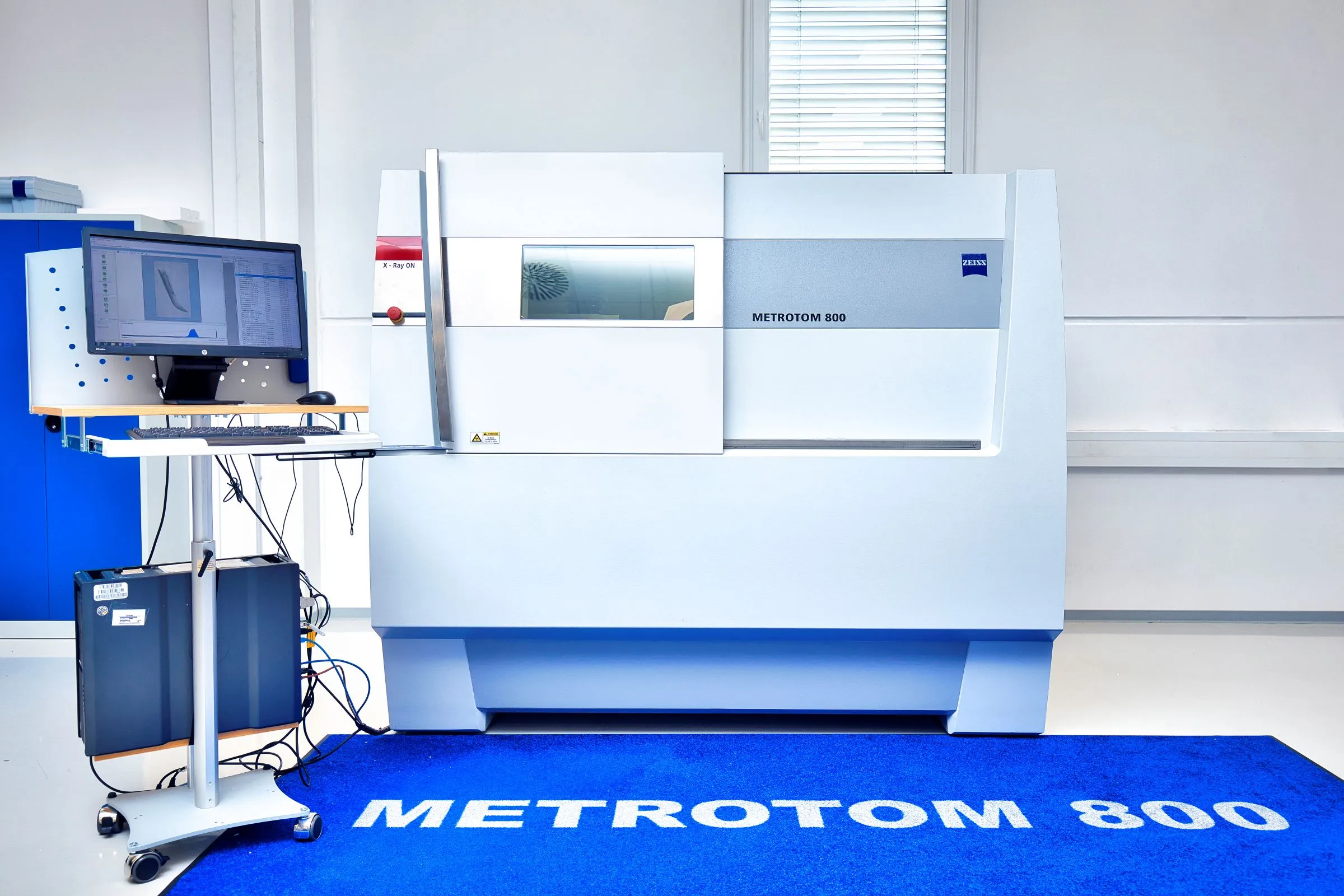
Wofür wird Industrielle Computertomographie genutzt?
Die industrielle Computertomographie (iCT) wird in vielfältigen Bereichen angewendet und zeigt erhebliche Vorteile in der Qualitätskontrolle und Produktentwicklung.
Ein Schlüsselbereich für die Nutzung der iCT ist die Fertigungsindustrie. Hier macht diese Technologie eine genaue Inspektion von Komponenten möglich, um sicherzustellen, dass sie den technischen Anforderungen entsprechen. iCT wird häufig verwendet, um Defekte und Unregelmäßigkeiten innerhalb bestimmter Materialien zu identifizieren und die Maßhaltigkeit von Bauteilen zu überprüfen.
Dazu zählen beispielsweise:
- Morphologische Eigenschaften von Bauteilen
- Poren und Lunker in Gussteilen
- Fasermerkmale von Kunststoffbauteilen
- Wandstärkenbestimmungen durch Soll-Ist-Vergleiche
Darüber hinaus wird die iCT im Bereich der Produktentwicklung eingesetzt, um die Design- und Fertigungsprozesse zu optimieren. Durch die Visualisierung des inneren Aufbaus eines Objekts können Ingenieure ein besseres Verständnis für das Verhalten des Bauteils unter verschiedenen Bedingungen erhalten.
Zuletzt findet die iCT auch Anwendung in der Archäologie, wo sie dazu dient, wertvolle Artefakte und Fossilien zu analysieren, ohne den wertvollen Fund physisch zu beschädigen.
Die industrielle Computertomografie bietet eine Reihe von Vorteilen, die sie zu einem wichtigen Werkzeug in verschiedenen Industrien und Forschungsbereichen macht. Nachfolgend sind einige Schlüsselvorteile aufgeführt:
- Zerstörungsfreie Prüfung: iCT schafft es, eine Untersuchung von internen Strukturen und Merkmalen von Objekten durchzuführen, ohne diese zu beschädigen oder zu zerlegen. Das ist besonders wertvoll bei der Prüfung von teuren oder einzigartigen Komponenten sowie in der Archäologie, wo Artefakte erhalten bleiben müssen.
- Präzise und detaillierte Visualisierungen: iCT liefert hochauflösende Bilder, die detaillierte Informationen über die innere Struktur eines Objekts liefern. Das ermöglicht eine genaue Analyse und Bewertung von Materialien und Komponenten.
- Zeit- und Kostenersparnis: Im Vergleich zu traditionellen Prüfmethoden kann iCT oft schneller und kosteneffizienter sein, da sie weniger manuelle Arbeit erfordert und gleichzeitig umfassendere Informationen liefert.
- Qualitätskontrolle und Fehlererkennung: Die Fähigkeit, Defekte und Unregelmäßigkeiten zu erkennen, die mit bloßem Auge oder durch andere Prüfmethoden nicht erkennbar wären, macht iCT zu einem wichtigen Werkzeug in der Qualitätskontrolle.
- Optimierung von Design und Fertigungsprozessen: Durch die Bereitstellung detaillierter Einblicke in das Verhalten von Materialien und Objekten unter verschiedenen Bedingungen, kann iCT dazu beitragen, Design- und Fertigungsprozesse zu verbessern.
-
Nachteile der Industriellen Computertomographie
Obwohl die industrielle Computertomografie zahlreiche Vorteile bietet, gibt es auch einige Herausforderungen und Grenzen, die beachtet werden sollten:
- Hohe Kosten: Die Anschaffung und Wartung von iCT-Geräten kann teuer sein, insbesondere für hochauflösende Systeme. Die Kosten können sich auch erhöhen, wenn spezielle Schulungen für die Bedienung der Geräte durch Mitarbeiter erforderlich sind.
- Zeitintensität: Während iCT in bestimmten Anwendungsbereichen Zeit sparen kann, fällt der Scanning-Prozess für komplexe oder große Objekte zeitaufwendig aus. Die Datenverarbeitung und -analyse können erhebliche Zeit in Anspruch nehmen, weil das Objekt von allen Seiten durchleuchtet werden muss.
- Materialgrenzen: Obwohl iCT eine breite Palette von Materialien untersuchen kann, gibt es Grenzen. Beispielsweise können sehr dichte Materialien, wie bestimmte Metalle, schwierig zu scannen sein und weniger detaillierte Ergebnisse liefern. Hierfür muss die Röntgenintensität erhöht werden, um das Material durchdringen zu können. In häufigen Fällen wird dann mehr Belichtungszeit benötigt, was wiederum die Messzeiten verlängert.
- Komplexität der Dateninterpretation: Die durch iCT generierten Daten können äußerst komplex sein und erfordern oft spezialisiertes Wissen für die korrekte Interpretation und Analyse. Hierfür sind gut ausgebildete Mess-Spezialisten vonnöten, die die Daten hinsichtlich ihrer Relevanz richtig einzuordnen wissen, um korrekte Rückschlüsse auf die technische Funktion des jeweiligen Bauteils zu liefern.
Anwendungen der Industriellen Computertomographie
Die industrielle Computertomographie (iCT) hat in einer Reihe von Branchen revolutionäre Anwendung gefunden. Dank ihrer Fähigkeit, das Innere von Objekten auf nicht invasive Weise darzustellen, ermöglicht sie einen tiefgehenden Einblick in die Struktur und Qualität von Komponenten und Materialien.
Vom Produktdesign über die Qualitätssicherung bis hin zur Schadensanalyse und Materialforschung - die iCT hat das Potenzial, Prozesse effizienter und genauer zu gestalten. In den folgenden Abschnitten werden wir uns einige spezifische Anwendungsgebiete ansehen, in denen die iCT ihre Stärken ausspielt.
Additive Fertigung
Die iCT wird in der additiven Fertigung häufig zur Qualitätskontrolle und Prozessoptimierung eingesetzt. Sie kann ein vollständiges 3D-Abbild des gedruckten Teils erstellen und dieses auf Unregelmäßigkeiten oder Defekte überprüfen. Das ist besonders wichtig in Branchen, in denen eine hohe Präzision von größter Bedeutung ist, wie zum Beispiel in der Luft- und Raumfahrt, im Automobilbau oder in der Medizintechnik.
Ferner liefert die iCT gute Resultate bei der Überprüfung des Pulverbetts im 3D-Drucker. Diese Informationen können dazu genutzt werden, den Druckprozess zu optimieren und so die Qualität des Endprodukts zu verbessern. Schließlich können durch die Verwendung der iCT auch postproduktive Analysen durchgeführt werden, um das Verhalten des Materials während des Druckprozesses zu verstehen und zu optimieren.
Weiche Materialien
Die iCT ist auch ein wichtiger Teil bei der Untersuchung weicher Materialien. Solche Materialien können beispielsweise biologisches Gewebe, Textilien oder Kunststoffe sein. Ihre Struktur ist oft komplex und fein. Herkömmliche Methoden können sie leicht beschädigen oder verändern. Daher bietet die iCT hier einen unschätzbaren Vorteil, da sie eine zerstörungsfreie Untersuchung ermöglicht.
Weiche Materialien können mit der iCT detailliert analysiert werden, indem man ihre innere Struktur visualisiert. Das erlaubt den Forschern, Parameter wie Größe, Form oder Verteilung zu bestimmen, was für das Verständnis der Materialeigenschaften entscheidend ist. In der Textilindustrie kann unter anderem die Struktur von Fasern untersucht werden, um ihre Qualität zu bewerten.
Tactile measurement technology
Die taktile Messtechnik ist eine traditionelle Methode zur Qualitätskontrolle sowie Inspektion von Bauteilen und konkurriert häufig mit der industriellen Computertomographie (iCT). Obwohl die taktile Messtechnik weiterhin in vielen Industrien eine wesentliche Rolle spielt, bietet die iCT mehrere entscheidende Vorteile.
Zunächst ermöglicht die taktile Messtechnik lediglich punktuelle Messungen auf der Oberfläche eines Bauteils. Im Gegensatz dazu liefert die iCT ein vollständiges 3D-Modell des Objekts, das sowohl die innere Struktur als auch die äußere Geometrie darstellt. Das lässt eine detailliertere und genauere Untersuchung des Bauteils zu.
Überdies ist die taktile Messtechnik zeitaufwendig und kann das Bauteil potenziell beschädigen oder verändern. Die iCT hingegen ist eine zerstörungsfreie Methode, die auch schneller durchgeführt werden kann. Insbesondere bei komplexen oder empfindlichen Bauteilen, wie sie in der Luft- und Raumfahrt oder der Medizintechnik häufig vorkommen, ist das von unschätzbarem Wert.
Allerdings gibt es auch Bereiche, in denen die taktile Messtechnik nach wie vor überlegen ist. Sie kann so etwa in bestimmten Situationen genauere Messungen liefern und ist oft günstiger in der Anschaffung und Wartung.
.webp)
Innere Strukturen von elektronischen und größeren Bauteilen
Die industrielle Computertomographie (iCT) spielt eine wichtige Rolle bei der Inspektion und Prüfung sowohl von elektronischen Bauteilen als auch von größeren Werkstoffen, indem sie eine detaillierte Darstellung ihrer internen Strukturen liefert.
Elektronische Bauteile sind oft klein und komplex, was ihre Prüfung zu einer Herausforderung machen kann. Mit der iCT können feinste Details innerhalb dieser Komponenten visualisiert und analysiert werden, ohne sie physisch zu beschädigen oder zu zerlegen. Das macht die iCT besonders effektiv in Branchen wie der Elektronikfertigung, wo sie zur Qualitätskontrolle, zur Fehlererkennung und zur Verbesserung von Produktionsprozessen beiträgt.
Größere Bauteile, wie sie in der Automobil- oder Luft- und Raumfahrtindustrie vorkommen, profitieren ebenfalls von der iCT. Trotz ihrer Größe erfordern diese Bauteile eine hohe Genauigkeit und Präzision, insbesondere bei der Inspektion von internen Strukturen oder versteckten Bereichen, die für herkömmliche Prüfmethoden schwer zugänglich sind. Die iCT erlaubt es, diese Bauteile in 3D zu visualisieren und bietet so einen detaillierten Einblick in ihre interne Geometrie und mögliche Mängel.
Obwohl die iCT für die Inspektion von inneren Strukturen in Bauteilen aller Größen verwendet werden kann, ist es wichtig, die richtige Auflösung und die richtigen Einstellungen auszuwählen, um optimale Ergebnisse zu erzielen. So können zuverlässige und wertvolle Daten zur Verbesserung von Produktqualität und Produktionsprozessen gewonnen werden.
Komplexe Bauteile und Dimensionelle Messtechnik
Die Dimensionelle Messtechnik und die Untersuchung komplexer Bauteile profitieren erheblich von der industriellen Computertomographie (iCT). Die iCT bietet eine Methode zur genauen, zerstörungsfreien und vollständigen Erfassung der Form und Dimensionen von Bauteilen, die wegen ihrer Komplexität mit herkömmlichen Messmethoden nur schwer zu erfassen sind.
In der Fertigungsindustrie wird die iCT zur Bestimmung der genauen Dimensionen von Bauteilen und zur Kontrolle der Einhaltung von Toleranzen eingesetzt. Sie schafft es, komplexe Bauteile, wie z.B. Spritzgussteile oder 3D-gedruckte Komponenten, vollständig zu vermessen und auf eventuelle Abweichungen zu prüfen. Im Vergleich zu taktilen Messmethoden erlaubt die iCT eine vollständige 3D-Vermessung der Bauteile, einschließlich der internen Strukturen.
Die iCT ist auch ein wertvolles Werkzeug zur Überprüfung der Einhaltung von Spezifikationen und zur Qualitätskontrolle. Mit ihrer Hilfe kann der Prüfer Bauteile schnell und effizient auf Maßgenauigkeit und Qualität überprüfen. So können Produktionsfehler minimiert und die Produktqualität verbessert werden.
Gescanntes Objekt und untersuchtes Objekt
Das gescannte Objekt spielt eine wesentliche Rolle in der industriellen Computertomografie. Seine Eigenschaften und Merkmale beeinflussen sowohl den Scanprozess als auch die Interpretation der erzeugten Bilder.
Je nach Materialzusammensetzung und Dichte des Objekts kann der CT-Scan unterschiedliche Tiefeninformationen liefern. Daher ist es wichtig je nach Werkstück die Parameter in dem Messvorgang einhergehend anzupassen.
Außerdem können die physischen Abmessungen und Eigenschaften des Objekts Einfluss auf den Scan-Vorgang haben:
Für einen CT-Scan muss das Werkstück von allen Seiten durchstrahlbar sein.
Ist das nicht der Fall, kommt es zu Problemen bei der Erstellung des 3D-Abbilds.
Dank der Flexibilität der iCT können aber die Scan-Parameter jederzeit verändert werden. So kann der Prüfer - wie bereits erwähnt - die Intensität der Röntgenstrahlung der Dichte des Materials anpassen.
Nach dem Scan-Vorgang kann das gescannte 3D-Abbild digital exportiert und zum Beispiel in ein CAD-Programm geladen werden, damit die Konstruktion gegebenenfalls Änderungen durchführen kann. Dieser Prozess wird als Reverse Engineering bezeichnet.
Innenliegende Strukturen mit einer hohen Anzahl an komplexer Innengeometrien
Die industrielle Computertomographie (iCT) hat sich als einzigartiges Instrument für die Untersuchung von Strukturen mit hoher Komplexität und einer großen Anzahl von Innen-Geometrien erwiesen. Solche Strukturen sind oft in Bereichen wie der Automobilindustrie, Luft- und Raumfahrt oder Medizintechnik zu finden, wo komplexe Bauteile, wie Motoren, Turbinen, Getriebe oder Implantate, gefertigt werden.
Im Gegensatz zu herkömmlichen Inspektionsmethoden ist die iCT in der Lage, eine zerstörungsfreie Prüfung der inneren Strukturen dieser Bauteile vorzunehmen. Sie liefert detaillierte 3D-Bilder der inneren Geometrien, die dann analysiert werden können, um Aspekte wie Form, Größe, Anordnung und Ausrichtung der Innenstrukturen zu bewerten.
Die Fähigkeit der iCT, Innenstrukturen in hoher Auflösung darzustellen, macht sie zu einem großartigen Werkzeug für die Qualitätssicherung und die Fehleranalyse. Sie macht es den Ingenieuren möglich, eventuelle Mängel oder Unregelmäßigkeiten im Inneren der Bauteile aufzudecken und zu beheben, bevor sie zu größeren Problemen führen.
Darüber hinaus kann die iCT auch verwendet werden, um den Fertigungsprozess von Bauteilen mit komplexen Innenstrukturen zu optimieren. Durch die Analyse der von der iCT gelieferten Daten können Ingenieure die Fertigungsprozesse verbessern und so die Qualität und Leistung der produzierten Bauteile steigern.
Es ist jedoch zu beachten, dass die iCT, trotz ihrer vielen Vorteile, eine komplexe Technologie ist, die sorgfältige Handhabung und Kalibrierung erfordert, um genaue und zuverlässige Ergebnisse zu liefern. Bei ordnungsgemäßer Anwendung ist sie jedoch ein hervorragendes Werkzeug zur Verbesserung der Qualität und Effizienz in zahlreichen Industriebranchen.
Messen von Regelgeometrie & Optische Systeme
Die industrielle Computertomographie (iCT) hat auch ihre Anwendungen in der Analyse von Regelgeometrien und optischen Systemen gefunden.
Regelgeometrien sind vereinfachte Formen, die oft in der technischen Zeichnung verwendet werden, um komplexe Geometrien darzustellen. Sie umfassen Grundformen wie Zylinder, Kegel, Kugeln und Quadrate. Mit der iCT können diese Regelgeometrien präzise gemessen und analysiert werden, wodurch mögliche Abweichungen und Fehler frühzeitig erkannt und behoben werden können. Das ist von entscheidender Bedeutung in Industrien, wo die Genauigkeit der Geometrien direkt mit der technischen Funktionalität des Bauteils zusammenhängt.
Optische Systeme, wie Linsen und Prismen, profitieren ebenfalls von der iCT. Diese Systeme erfordern eine extrem hohe Genauigkeit bei der Fertigung, da kleinste Unregelmäßigkeiten zu erheblichen Leistungseinbußen führen können. Die iCT erlaubt zudem eine detaillierte und zerstörungsfreie Inspektion dieser Komponenten. Sie kann verwendet werden, um Aspekte wie die Dicke der Linsen, die Ausrichtung der optischen Achsen und das Vorhandensein von internen Defekten zu überprüfen.
Eine weitere nützliche Anwendung der iCT in der Optik ist die Analyse und Verbesserung von Beleuchtungssystemen. Mithilfe von iCT können Lichtpfade analysiert und optimiert werden, was zu einer verbesserten Effizienz und Leistung des Beleuchtungssystems führt.
Es ist jedoch wichtig zu verstehen, dass die Anwendung der iCT auf Regelgeometrien und optische Systeme besondere Anforderungen an die Systemkalibrierung stellt. Aus diesem Grund sollte sie nur von Fachleuten mit entsprechender Ausbildung und Erfahrung durchgeführt werden, um genaue und zuverlässige Ergebnisse zu gewährleisten.
Conclusion
Die industrielle Computertomografie hat sich als revolutionäre Technologie in vielen Industriebereichen durchgesetzt. Sie bietet einzigartige Vorteile in der Inspektion und Analyse verschiedener Materialien und Komponenten. Die additive Fertigung, weiche Materialien, elektronische Bauteile und komplexe Werkstücke sind nur einige Aspekte, in denen die iCT glänzt. Trotz einiger Nachteile, wie den hohen Kosten und der Notwendigkeit spezialisierter Fachkenntnisse, überwiegen die Vorteile dieser Technologie deutlich.
In der Zukunft werden wir sehen, wie sich die industrielle Computertomografie noch weiterentwickeln wird und in neue Bereiche vordringt. Mit weiteren Fortschritten in der Technologie und dem Potenzial für sinkende Kosten könnte die iCT eine noch wichtigere Rolle in der industriellen Inspektion und Qualitätssicherung spielen. Sie hat das Potenzial, die Art und Weise, wie wir Produkte herstellen und testen, zu revolutionieren und bietet spannende Möglichkeiten für weitere Messverfahren und -techniken.