Die optische Messtechnik spielt eine wichtige Rolle bei modern-industriellen Fertigungsprozessen. Gerade die hohe Messgeschwindigkeit kennzeichnet diese Verfahren.
Wie funktioniert die optische Messtechnik im Detail? Die optische Messtechnik basiert auf der Verwendung von Licht. In erster Linie werden Längen, Formen und Oberflächen gemessen. Im Vergleich zu taktilen Messsystemen können optische Verfahren mit einer deutlich höheren Geschwindigkeit durchgeführt werden. Hinzu kommt, dass die Messung berührungslos erfolgt, sodass empfindliche Bauteile nicht beschädigt werden. Für die Messung können optische 2D- und 3D-Messsysteme eingesetzt werden.
Wir bei Q-Tech verwenden 2D-Videomessmikroskope, einen 3D-Scanner und eine ZEISS O-Inspect, die taktile und optische Messmethoden miteinander verbindet. Sie wollen mehr zu den einzelnen Messgeräten wissen? Dann erhalten Sie in diesem Artikel weitere Informationen.
Grundlagen & Anwendungen
Bei automatisierten optischen Messungen können Bauteile innerhalb von Sekunden vermessen werden. Sogar das Erfassen von ganzen Flächen innerhalb von Millisekunden ist möglich. Somit haben optische Messverfahren aufgrund des zeitlichen auch einen wirtschaftlichen Vorteil gegenüber dem taktilen Messen.
Die optische Messtechnik findet in der Automobilindustrie, der Luft- und Raumfahrtindustrie, der Medizintechnik, der Elektroindustrie und der Werkzeugherstellung Verwendung.
Die gängigsten Anwendungen sind die folgenden:
- Qualitätskontrolle: Die detaillierte Vermessung der Bauteile garantiert, dass die Produkte den spezifischen Anforderungen entsprechen.
- Reverse Engineering: Auf der Basis der vollflächigen Erfassung der Bauteile können CAD-Modelle erstellt und so beispielsweise Ersatzteile reproduziert werden.
- Formanalyse: Durch optische Verfahren lässt sich die Form von Werkstücken analysieren und leichter optimieren.
- Oberflächenanalyse: Die Vermessung von Oberflächen gibt Aufschluss über die Rauheit, Textur und andere Eigenschaften eines Bauteils.
Welche optischen Messverfahren gibt es?
Werfen wir nun einen Blick auf die optischen Messverfahren. Während viele vor allem das Laserscanning kennen, gibt es dennoch eine ganze Reihe an unterschiedlichen optischen Verfahren zur Beurteilung von physikalischen Größen.
Laserscanning
Aufgrund seiner Film- und Fernsehpräsenz erlangte das Laserscanning einen hohen Bekanntheitsgrad, allerdings hat es im Bereich der 3D-Messtechnik nur einen geringen Stellenwert.
Während des Vorgangs fährt ein Laserstrahl an der Oberfläche des Werkstücks entlang und die Reflexion wird über einen Fotosensor wieder detektiert. Damit das Bauteil vollständig erfasst werden kann, muss entweder das Objekt oder der Scanner bewegt werden.
Da Maschinen in der Regel eine Kalibrierung benötigen, bevorzugen viele Prüfer die Bewegung des Objekts.
Eines der Haupteinsatzgebiete ist das oben genannte Reverse Engineering. Hierbei werden die benötigten Objekte gescannt und somit der Grundbaustein für die CAD-Modelle gelegt. Eine weitere häufige Verwendung ist der Modelldruck mit additiven Verfahren, wie zum Beispiel der 3D-Druck.
Auch private Endverbraucher können sich bereits für kleines Geld ein optisches Messgerät mit Laserscanning kaufen. So sind moderne 3D-Drucker manchmal bereits mit Lasern ausgestattet.
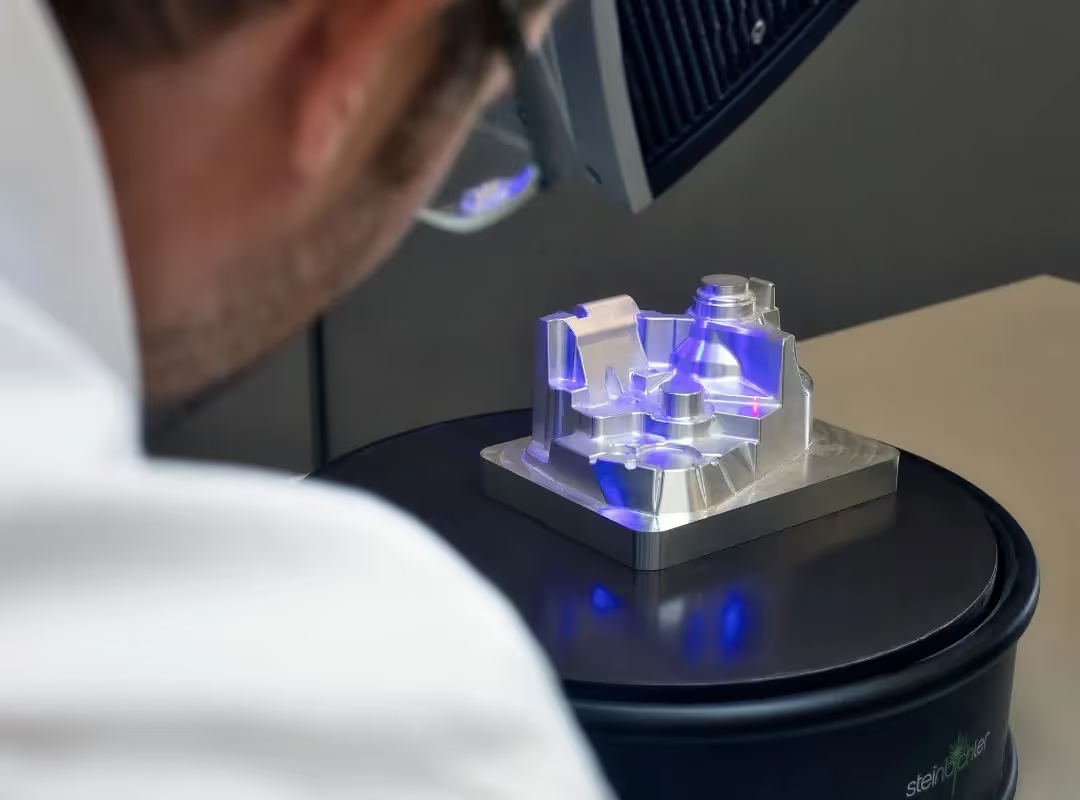
Lichtlaufzeit
Die Astronomie war der Ursprung für das optische Messen mit der Lichtlaufzeit. Eine bekannte Anwendung ist hier die Distanzmessung von Himmelskörpern.
Diese Messtechnik kommt nach und nach auch in der Industrie an, kann aber mit den anderen bekannten Verfahren bei der Bauteilkontrolle noch nicht mithalten.
Streifen- und Musterprojektion
Die Streifen- und Musterprojektion ist im industriellen Bereich neben der klassischen Messtechnik vor allem im Karosseriebau und bei der Instandsetzung kleinerer Blechschäden bekannt. Hierbei projiziert das optische Messgerät ein Muster auf das Bauteil. Selbst bei kleinsten Störungen der Oberfläche verziehen sich die Streifen bzw. Quadrate deutlich. Der Prüfer kann so Beulen und Dellen leicht erkennen und entsprechende Lösungsansätze einleiten.
Zusätzlich lassen sich durch Oberflächenmessungen die Toleranzabweichungen deutlich machen.
Im Anschluss kommen Ausbeulwerkzeuge zum Einsatz. Kommt es in der Industrie zu einer größeren Toleranzabweichung bei einem geprüften Bauteil, wird dieses ausgesondert und muss nachgearbeitet werden.
Für die Streifen- und Musterprojektion benötigt man einen Musterprojektor, eine Erfassungskamera, ein Auswertungsprogramm und eine Kalibrierfläche.
Fokus-Variation
Eigentlich kennt man die Fokus-Variation eher aus der Kameratechnik, aber sie kommt auch in der Messtechnik zum Einsatz – insbesondere bei der Oberflächenanalyse. Das Messen von Rauheit und Profilen gestaltet sich hiermit als einfach und schnell.
Die Fokus-Variation kann einen Messbereich auf einmal erfassen und muss ihn nicht erst abscannen. Das macht sie zu einer der schnellsten optischen Messmethoden überhaupt. Viele optische Messgeräte mit Fokus-Variation ersetzen nach und nach Messgeräte aus der taktilen Messtechnik.
Konfokale Messtechnik & Weißlichtinterferometrie
Bei der konfokalen Messtechnik wird das Prüfobjekt mit einer sehr kleinen Blende angestrahlt. Die Blende sitzt auf einem schräg angeordneten Spiegel. Dieser Spiegel wird genutzt, um das reflektierte Licht umzuleiten und durch eine weitere gerade angeordnete Blende zu schicken.
Hinter der Blende befindet sich ein empfindlicher Lichtsensor. Trifft der Brennpunkt des Lichts auf die Oberfläche, entsteht eine hohe Lichtintensität. Das Ganze passiert, wenn das Objekt durch den Strahlengang der Lichtquelle geführt wird.
Ist der genannte Brennpunkt oberhalb oder unterhalb, lässt die Intensität der Reflexion nach.
Die Lichtschwankungen werden von einem Sensor erfasst und in einen Messwert umgerechnet.
Konfokale Messmethoden und Weißlichtinterferometrie eignen sich hervorragend für die Erfassung von Toleranzen im Mikrometerbereich.
Stereofotografie
Die Stereofotografie ist eine einfache Form der Streifenprojektion. Dabei wird ein Werkstück gleichzeitig von zwei nah beieinander liegenden Kameras fotografiert. Anschließend verwandelt der Computer die digitalen Fotos in gerenderte Objekte.
Jedoch kann die Stereofotografie nicht mit der Genauigkeit einer Streifenprojektion mithalten. Demzufolge ist die industrielle Relevanz bei der Stereofotografie deutlich niedriger.
Für den Bereich der Gesichtserkennung oder der Anpassung maßgeschneiderter Kleidung ist die Stereofotografie jedoch eine sehr zuverlässige Methode.
Messwerkzeuge bei Q-Tech
Bei Q-Tech kommen nicht alle der oben genannten Methoden zum Einsatz. Welche Messwerkzeuge und Methoden bei uns verwendet werden, erfahren Sie im Folgenden.
2D-Videomikroskop (OGP SmartScope Flash 200)
Das 2D-Videomikroskop von OGP ist ein vollwertiges automatisches Messsystem, das umfangreiche Messmöglichkeiten bietet. Charakteristisch für das SmartScope Flash 200 ist die Hebebrücke, die dafür sorgt, dass das System auf dem Tisch nur wenig Platz einnimmt.
Ein eingebautes LED-Ringlicht liefert die perfekte Flexibilität für die Oberflächenbeleuchtung. Unterstützt wird das Ganze von einem LED-Array-Hintergrundlicht.
ZEISS O-Inspect
Das ZEISS O-Inspect ist eine Kombination aus optischen und taktilen Sensoren. Das Messgerät bietet ein großes Sichtfeld mit hoher Bildschärfe, schnelle und präzise taktile 3D-Messungen und optische Messungen für empfindliche Oberflächen.
Hinzu kommt die Software CALYPSO von ZEISS, die dank des intuitiven Bedienkonzepts und der Funktionsvielfalt auf ganzer Linie überzeugt.
3D-Scanner (GOM ATOS Q 8M)
Zu guter Letzt besitzt Q-Tech den 3D-Scanner ATOS Q von GOM. Dieser Scanner ist sehr vielseitig und hervorragend geeignet für komplexe Mess- und Inspektionsaufgaben. Selbst hohe messtechnische Ansprüche sind für den ATOS kein Problem.
Der Erfolg der ATOS-Sensoren liegt in der präzisen Optoelektronik, dem robustem Sensordesign und einer umfassenden Software.
Die Linsen lassen sich einfach austauschen und liefern somit noch flexiblere Arbeitsmöglichkeiten. Bei kleinen bis mittelgroßen Werkstücken macht dem ATOS Scanner niemand etwas vor.
Eine Übersicht zu unserem gesamten Equipment finden Sie hier.
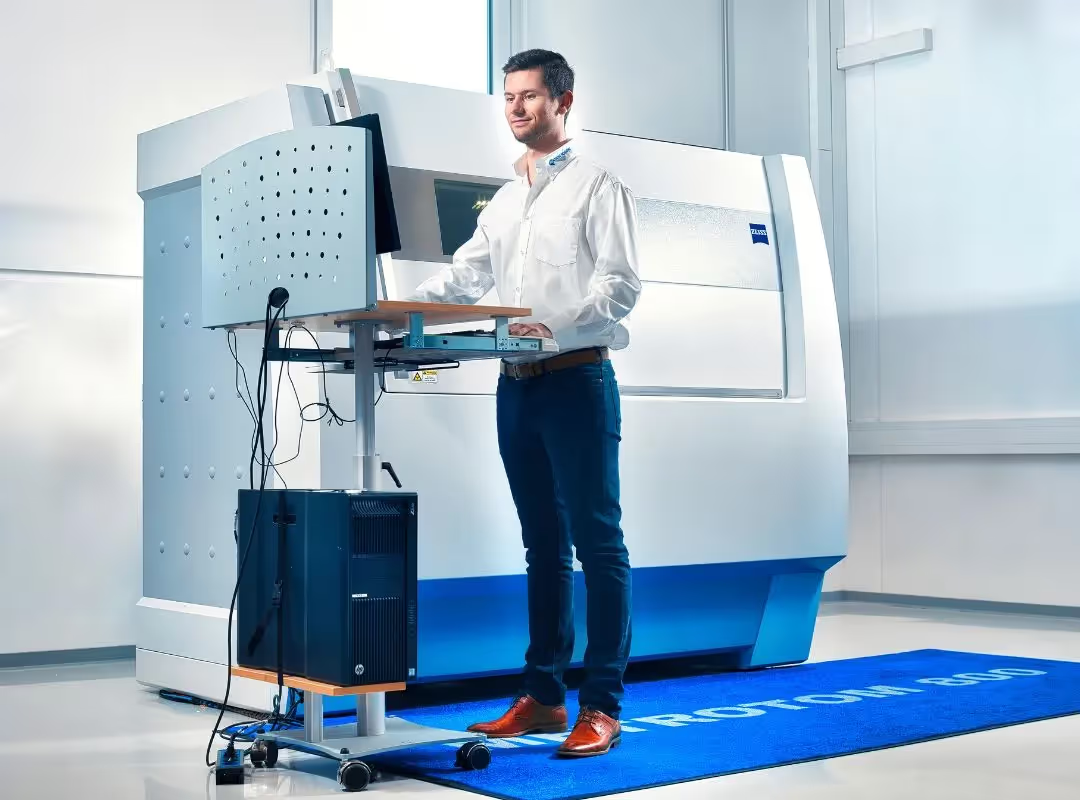
Vorteile der optischen Messtechnik
Jetzt kennen Sie die einzelnen Verfahren der optischen Messtechnik. Im Folgenden sind noch einmal die wichtigsten Vorteile zusammengefasst, die optische Systeme mit sich bringen:
- Geschwindigkeit: Es können ganze Flächen in Sekundenbruchteilen gemessen werden. Taktile Systeme brauchen hier deutlich länger, da sie von Punkt zu Punkt messen.
- Berührungslose Durchführung: Optische Systeme messen aus der Distanz, was sowohl eine Beschädigung empfindlicher Bauteile als auch einen Einfluss auf den Messwert verhindert.
- Präzision: Die Auflösung und Messgenauigkeit bei optischen Systemen ist meist sehr hoch.
- Flexibilität: Optische Systeme lassen sich nahezu überall einsetzen - egal ob Qualitätskontrolle oder Reverse Engineering
Die optische Messtechnik in der Zukunft
Die optische Messtechnik wird in der Zukunft in der Industrie eine immer wichtigere Rolle einnehmen.
Gekennzeichnet ist dieser Entwicklungsprozess z. B. durch die Integration von optischen Messsystemen in Fertigungsprozesse, die Verwendung von künstlicher Intelligenz zur Analyse von Messdaten und die Entwicklung von mobilen und tragbaren Messsystemen.
Fazit: Die optische Messtechnik ist ein unverzichtbarer Bestandteil moderner industrieller Prozesse
Die moderne optische Messtechnik wird in Zukunft industrielle Fertigungsprozesse mehr und mehr unterstützen. Sie bietet eine hohe Geschwindigkeit, Präzision und Flexibilität bei der Vermessung von Bauteilen.
Unsere Messgeräte ZEISS O-Inspect und GOM ATOS Q 8 M sind ein anschauliches Beispiel für optische Messsysteme, die sehr flexibel sind und dadurch in unterschiedlichen Branchen zum Einsatz kommen.