Die 3D-Koordinatenmesstechnik zählt zu den präzisesten Prüfverfahren überhaupt. Aufgrund der hohen technischen Anforderung kommt sie vor allem bei Prototypen, Einzelstücken und Stichproben zum Einsatz. Die Bauteile können mit absoluter Genauigkeit in ihrer Gesamtheit erfasst werden. Zwei wichtige Vertreter in diesem Bereich sind taktile und optische Messverfahren.
Was ist die 3D-Koordinatenmesstechnik? Die 3D-Koordinatenmesstechnik ermittelt dreidimensionale Koordinaten mithilfe eines Messarmes, einer Koordinatenmessmaschine oder eines optischen Scanners. Die erzielte Messgenauigkeit liegt im Mikrometerbereich. Sie zählt zu den präzisesten Varianten in der Industrie. Die erzeugten Messdaten dienen anschließend als Basis zur Erstellung von Messprotokollen und als Fundament für die Qualitätskontrolle.
In dem Hause Q-Tech übernimmt die 3D-Koordinatenmesstechnik einen wichtigen Part. In diesem Artikel erfahren Sie mehr zur Funktionsweise der Maschinen und welche bei uns zum Einsatz kommen.
Grundlagen & Funktionsweise
Die Technologie wird verwendet, um Objekte in einem dreidimensionalen Koordinatensystem zu messen. Hierfür kommen verschiedene Geräte zum Einsatz. Das können Koordinatenmessmaschinen, Portalmessmaschinen, Laserscanner und optische Systeme sein.
Mithilfe dieser technischen Möglichkeiten ist es realisierbar, komplexe Formen und Geometrien zu erfassen und mit höchster Genauigkeit zu messen.
Während des Vorgangs erfasst die Maschine die Position eines Objekts im Raum und bestimmt die Koordinaten der einzelnen Punkte. Das Ganze geschieht mit der Verwendung von den drei Koordinatenachsen: X, Y und Z. Diese Achsen sind in einem kartesischen Koordinatensystem angeordnet.
Einige moderne Geräte in der 3D-Koordinatenmesstechnik verwenden auch eine Kombination aus taktilen und optischen Messmethoden, um eine höhere Messgenauigkeit zu erzielen.
Bei der taktilen Variante berührt ein Taster das zu messende Bauteil an den verschiedenen Punkten. Der Taster erfasst die Position der Punkte und gibt die Information an das Messgerät zurück.
Bei den optischen Methoden kommt ein Laserstrahl oder eine Kamera zum Einsatz, um die Oberfläche des Bauteils zu scannen und für die nachgelagerte Vermessung zu digitalisieren.
Areas of application
Koordinatenmesstechnik wird in der Qualitätskontrolle, der Produktentwicklung und der industriellen Fertigung angewendet. Relevante Industriegebiete sind die Luft- und Raumfahrt, die Automobilindustrie und die Medizintechnik.
Heutzutage sind solche präzisen Messungen unerlässlich für die Überprüfung bestimmter Spezifikationen und die Verbesserung der Produktqualität.
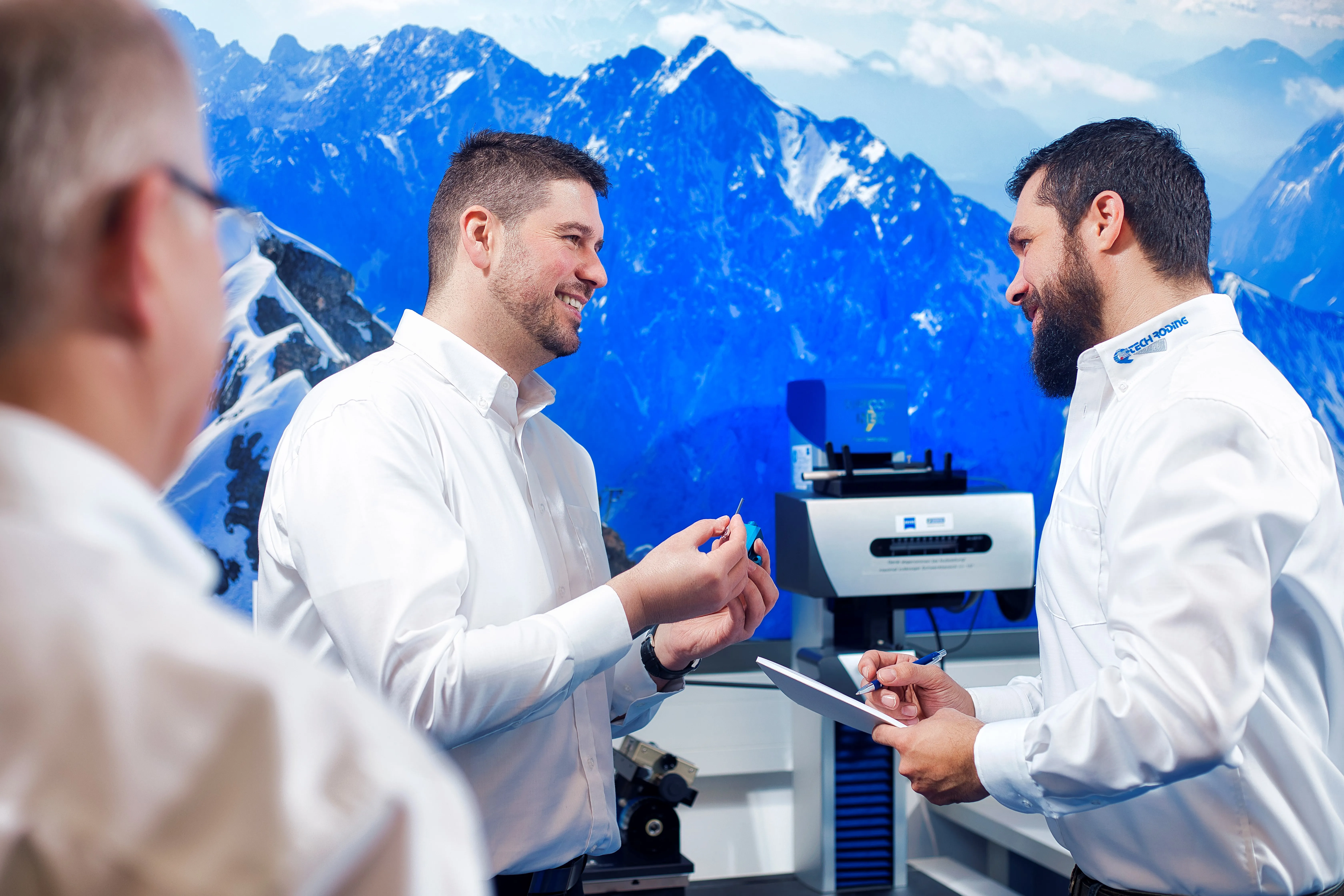
Vorbereitung für die Messung
Eine Messung mit einem 3D-Koordinatenmesssystem bedarf einer genauen Vorbereitung. Unter anderem, weil in diesem Bereich die Messtechniker hochgenaue Maße überprüfen. Daher haben auch äußere Faktoren einen großen Einfluss auf die Messung.
Wichtig sind vor allem:
- Eigenschaften des Messkopfs: Je nach Messsystem können unterschiedliche Tastköpfe zum Einsatz kommen. Diese unterscheiden sich in Form, Durchmesser und Größe. Dabei sind die Kennzeichen des Bauteils entscheidend dafür, welcher Messkopf genutzt wird. Vor dem Beginn der Messung muss der Messtechniker einen geeigneten Messkopf wählen.
- Umgebungstemperatur/Werkstücktemperatur: Dieser Parameter ist einer der entscheidenden in der Vorbereitung. Der Grund ist, dass insbesondere Metalle sich unter Wärmeeinfluss ausdehnen und bei Kälte wieder zusammenziehen. Bei einem größeren Bauteil sind die entstehenden Kräfte und Formabweichungen umso gravierender. Aufgrund dieser physikalischen Gegebenheiten ist der ideale Platz für eine Messung, ein klimatisiertes Labor und ein Temperschrank. In diesem bringt man das Bauteil auf die ideale Messtemperatur. Dadurch werden jegliche Formabweichungen durch Wärmeeinfluss ausgeschlossen.
- Luftfeuchtigkeit: Ein weiterer Störfaktor kann die Luftfeuchtigkeit sein. Ist diese zu hoch, verlieren die Messköpfe an Präzision. Das kann beim Prüfvorgang die Ergebnisse verfälschen. Genau wie bei der Umgebungstemperatur auch können hier Temperschrank und Klimaanlage helfen, diesen Störfaktor zu eliminieren.
Kalibrierung der Taster
Ein weiterer wichtiger Punkt in der Vorbereitung ist die Kalibrierung der Tastspitzen. Denn die Messdaten werden in erster Linie durch eine Antastung des Bauteils mit einem Taster erfasst, der an der Messachse des Geräts angebracht ist.
Relativ gesehen zum Koordinatensystem der Maschine, muss die Position der Spitze vor der Messung genau bestimmt werden. Das Bauteil wird mit der Kante der Tastspitze angetastet. Im Vorfeld muss der Prüfer den Mittelpunkt und den Radius der Tastspitze durch die Messung einer absolut exakt-definierten Kalibrierkugel bestimmen.
Ist dieser Vorgang abgeschlossen, bereinigt die Maschine bzw. die Software die Koordinaten der Spitze mathematisch um den Radius. So wird der tatsächliche Berührungspunkt berechnet, sobald die Maschine ein Werkstück antastet. Die Richtung dieses “Versatzes” ermittelt die Maschine automatisch.
Advantages
Nachdem Sie nun die Arbeitsweise einer Koordinatenmessmaschine vor Augen haben, lernen Sie die einzelnen Vorteile kennen, die sich durch diese Messmethode ergeben.
- Präzision: Richtig kalibriert und programmiert, ermöglicht die 3D-Koordinatenmesstechnik eine hochpräzise Messung von Bauteilen. Die Daten werden von einer Software verarbeitet, um den Ist-Zustand des Bauteils zu ermitteln. Im Anschluss können so die Abweichungen in der Größe, Länge, Form und Lage zu den Soll-Werten berechnet werden.
- Schnelligkeit: Der ganze Messvorgang läuft verhältnismäßig schnell ab. Das ist insbesondere in der Fertigung sehr vorteilhaft, weil so die Messzeit verkürzt wird und die Wirtschaftlichkeit steigt.
- Flexibilität: Die Technologie eignet sich hervorragend für Anwendungen in der Automobil- und Elektroindustrie, dem Maschinenbau und der Luftfahrt. Dank der hohen Präzision ist die Methode auch bei der Herstellung medizinischer Geräte einsetzbar.
- Automation: Eine vollständige Automation ist definitiv möglich. So kann eine Messung schnell, zuverlässig und reproduzierbar erfolgen. Das bedeutet, dass mehrere gleiche Bauteile mehrfach in der gleichen Position und Ausrichtung gemessen werden können. Automatisierte Prozesse reduzieren die Wahrscheinlichkeit menschlicher Fehler und sorgen für eine erhöhte Qualität der Messergebnisse.
Die Messmethode in der Zukunft
Der Innovationsdruck in diesem Bereich der Messtechnik ist besonders hoch.
Momentan ist das taktile 3D-Koordinatenmessgerät weiterhin der Industriestandard. Andere Messtechnologien konnten sich aber bereits als mögliche Alternativen am Markt etablieren. Allerdings ist zu erkennen, dass viel für berührungslose Verfahren spricht.
Mittlerweile werden auch taktile und optische Messmethoden miteinander kombiniert, um aussagekräftigere Ergebnisse zu erzielen. Des Weiteren brauchen insbesondere ältere taktile Verfahren deutlich mehr Zeit als optische Varianten. Aus diesem Grund wird bei entsprechend geeigneten Bauteilen und Toleranzen die Messung im 3D-Koordinatensystem oft mit fotometrischen Verfahren durchgeführt.
Anstatt einem 3D-Koordinatenmessgerät kommen dann z. B. zwei Digitalkameras zum Einsatz. Der Rechner generiert nach dem Fotografieren des Bauteils ein digitales Abbild, welches frei in einem 3D Koordinatensystem dargestellt wird. Anschließend kann der Prüfer den digitalen Körper in der Software drehen und vermessen.
Neben den genannten fotometrischen Verfahren gibt es auch noch andere optische Methoden in der 3D-Koordinatenmesstechnik:
- Streifenprojektion
- Liniensensoren
- Laserscanning
- Grauwertauswertung
- Kontrastverfahren
- Konfokal- und interferometrische Sensoren
- Stereoskopische Digitalfotografie
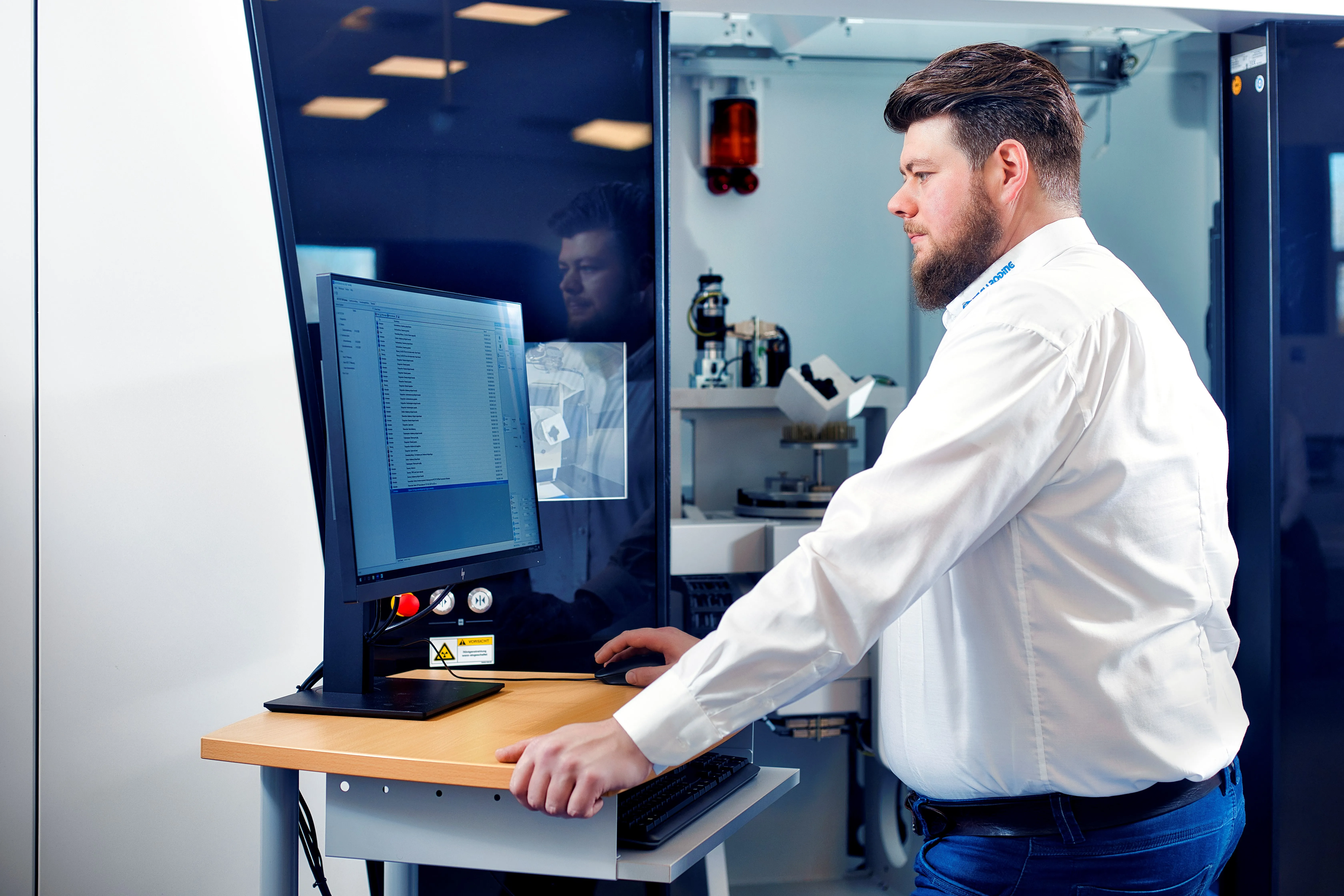
3D-Koordinatenmesstechnik bei Q-Tech
Im Hause Q-Tech bieten wir maßgeschneiderte 3D-Koordinatenmessungen für unsere Kunden an.
Wir setzen dabei auf Maschinen des Herstellers ZEISS. Die Maschinen PRISMO ULTRA, PRISMO VERITY, ACCURA 7 und ACCURA II nutzen moderne taktile Sensoren zur Ermittlung von Maß- und Formabweichungen.
Mit der O-Inspect 863 haben wir auch eine Maschine mit im Portfolio, die optische Verfahren mit der taktilen Methode in einem System kombiniert.
Als qualitativ hochwertige Messsoftware wird bei uns CALYPSO verwendet.
Die entscheidende physikalische Größe, die wir bei Q-Tech messen, ist die Länge. Wir sind also Dienstleister für Längenmesstechnik. Hierfür eignen sich unsere Maschinen hervorragend, weil sie hochpräzise und aussagekräftige Vermessungen ermöglichen.
Herausforderungen und Grenzen
3D Koordinatenmessmaschinen eignen sich exzellent für die Prüfung von Maßen, Winkeln, sowie Form- und Lagetoleranzen.
Bedenken Sie aber, dass mit einer Koordinatenmessmaschine ein Bauteil nur von außen geprüft werden kann. Störungen bzw. Fehler im Inneren bleiben meist unentdeckt und sind nicht detektierbar.
Hierfür eignet sich insbesondere die industrielle Computertomografie, die auch das Innere von Bauteilen erfassen kann und dort Störungen wie Risse, Lunker, Einschlüsse oder Poren ausfindig macht.
Sie haben Interesse an unseren Computertomografen oder an unserer 3D-Koordinatenmesstechnik? Dann werfen Sie einen Blick auf unser Equipment.
Conclusion
Die 3D-Koordinatenmesstechnik ist heutzutage das Nonplusultra bei industriellen Messverfahren.
Konturen, Längen sowie Form- und Lagetoleranzen lassen sich äußerst präzise mit diesen Messverfahren messen. Jedoch ist zu beobachten, dass optische Messverfahren sich am Markt deutlich stärker etablieren.
Daher setzen viele Hersteller auf die Kombination von optischen und taktilen Messmethoden und arbeiten stets daran, die etablierten Verfahren durch noch leistungsfähigere Ansätze zu verbessern.
Der Messdienstleister Q-Tech bietet Ihnen perfekt zugeschnittene Messtechnologien, die allen heutigen modernen Standards entsprechen und somit aussagekräftige und präzise Messergebnisse liefern.
Unserem qualifizierten Fachkräfte-Team liegt es sehr am Herzen, Ihnen das bestmögliche Messergebnis für Ihre Bauteile zu liefern, damit Sie sich der Qualität der gefertigten Werkstücke vollkommen sicher sein können.